NanoXplore / René Matériaux Composites (RMC)
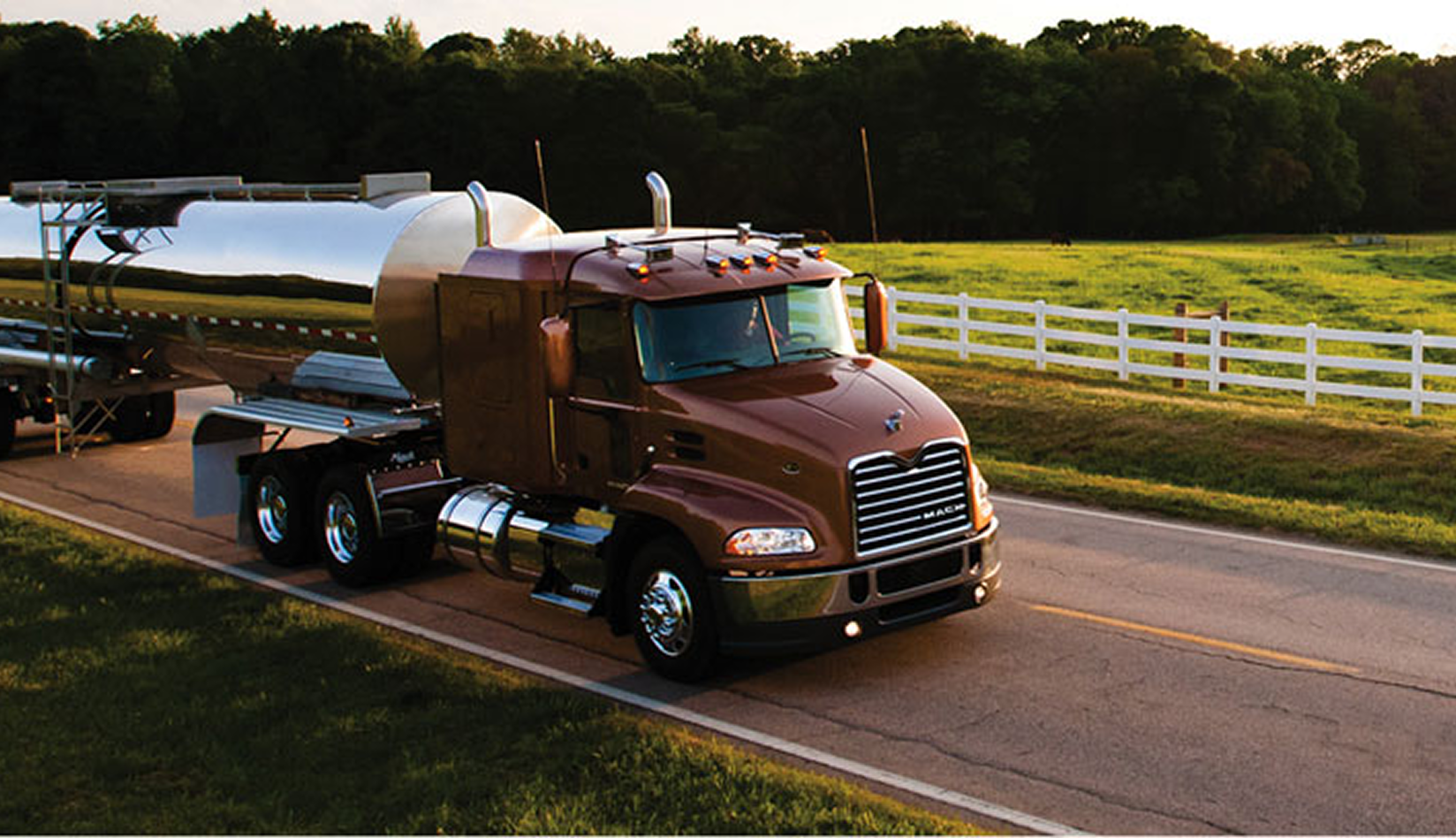
The context
Quebec-based René Matériaux Composites (RMC), a NanoXplore company, manufactures high-quality truck parts, like bumpers, using moulded plastic and composite materials. Before shipping, each part is primed and inspected to ensure it’s free of defects—such as pinholes, scratches, or blisters—that could affect the client’s final paint finish. Currently, quality control involves two manual inspections: first, defects are visually identified, circled in chalk, and corrected; then, during a second inspection, corrections are verified by checking logged data in the system (e.g. a small scratch in zone two). To boost inspection accuracy, streamline defect tracking, and reduce time spent on manual checks, RMC sought an upgrade to their existing Quality Management System for seamless defect recording, visualization, and analytics.
Project details
The challenge
RMC’s previous Quality Management System required inspectors to move between the part being inspected and a computer, creating opportunities to enhance efficiency, data consistency, and ease in locating original defects during final visual inspection. Additionally, RMC aimed to improve analytics to better track recurring defect patterns and support smooth worker adoption.
Our challenge was to design a solution that guided inspectors to specific defect areas, improved data reliability, and laid the groundwork for future AI-driven quality control. RMC aimed to incorporate an augmented reality (AR) headset that would allow hands-free, intuitive defect tracking directly on the part, reducing delays and setting the stage for AI defect detection.
The task at hand
We began by visiting RMC’s factory to observe the inspection process and common defect types. After discussions with workers and stakeholders, they expressed an interest in trying something with Microsoft’s HoloLens 2 AR headset, and so we proposed our AR solution for tagging defects (though this solution could be adapted for other AR headsets). This concept was enthusiastically received, prompting us to design and test a prototype with continuous feedback from inspectors.
We developed an AR app that allows inspectors to tag defects directly onto parts using a 3D CAD model of the bumper, which they interact with through intuitive hand gestures. Inspectors can mark defect locations on the real part while the app precisely maps these actions to the digital model. Drawing from gaming technology, the interface accurately tracks each defect’s location with a “pinching” gesture, creating a smooth, interactive experience.
During final inspection, the app overlays visual markers on the part to confirm defect corrections, adding precision and reliability to the process. The HoloLens 2 allows inspectors to log data hands-free, streamlining defect recording and data collection.
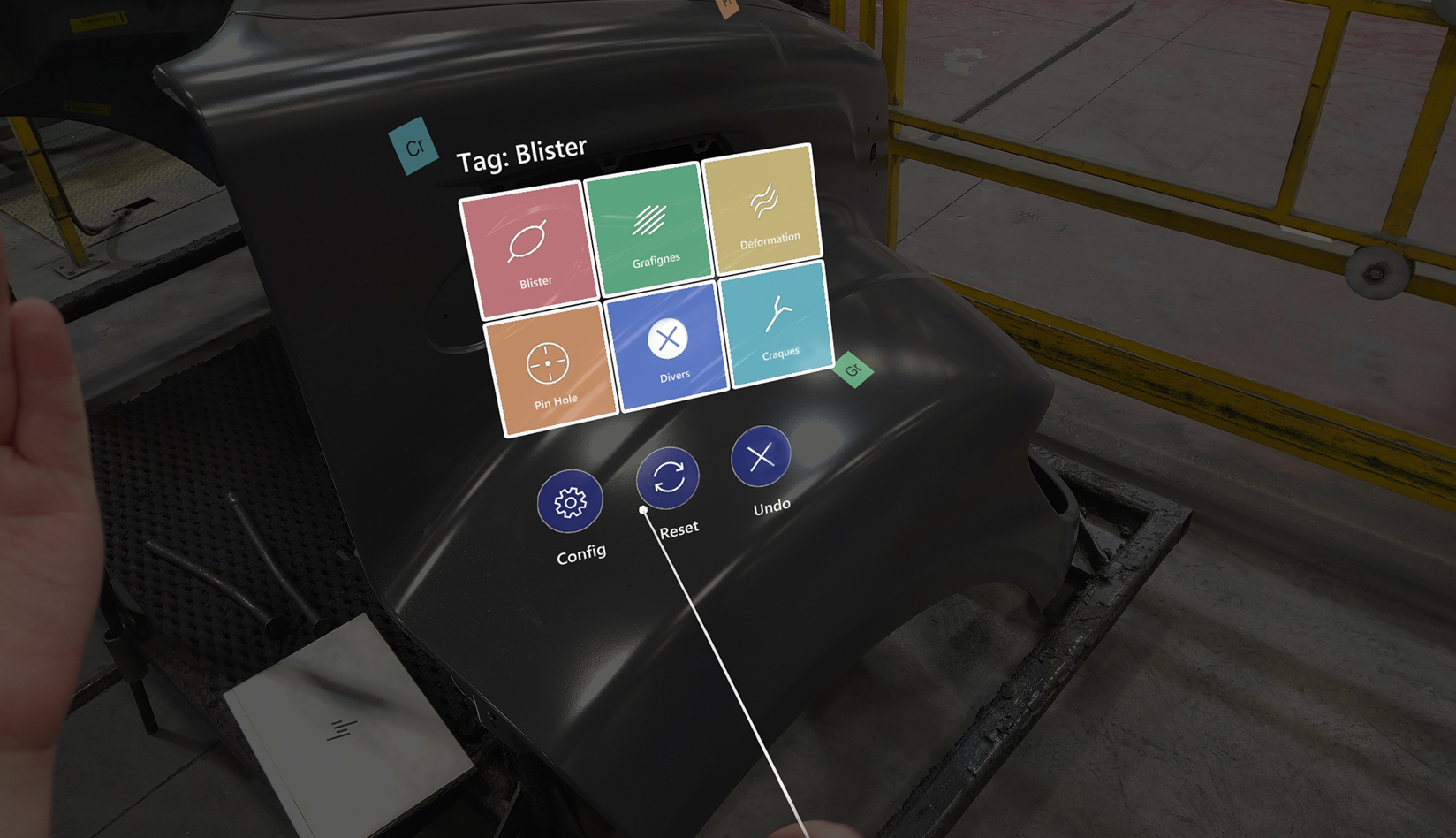
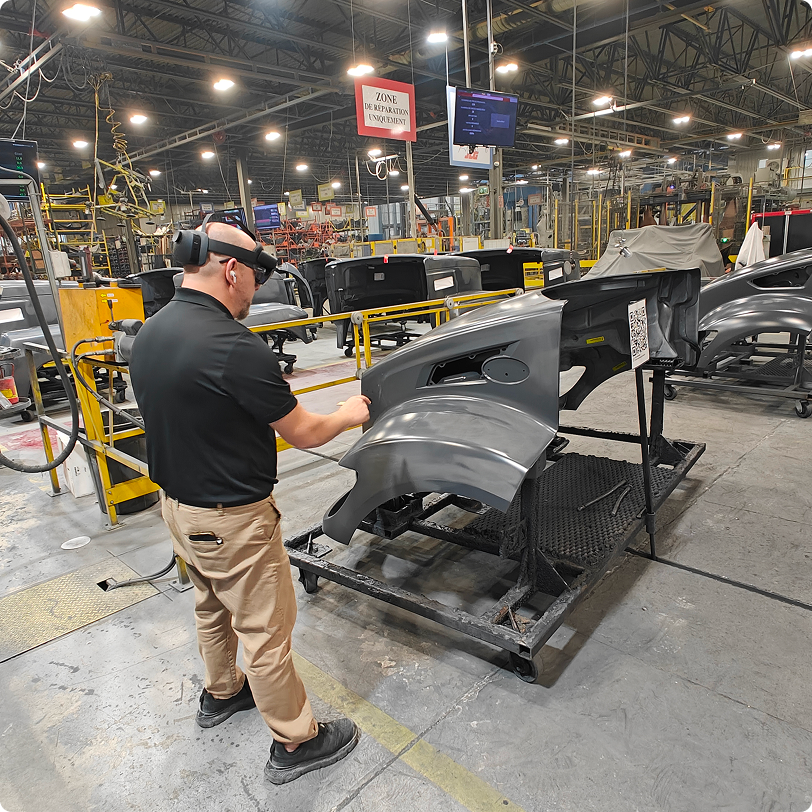
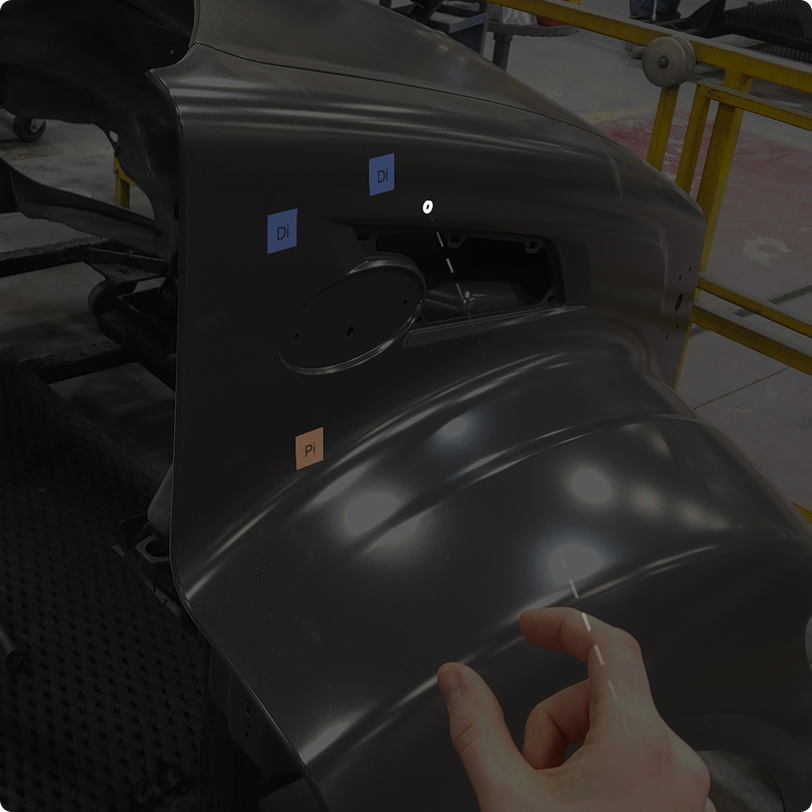
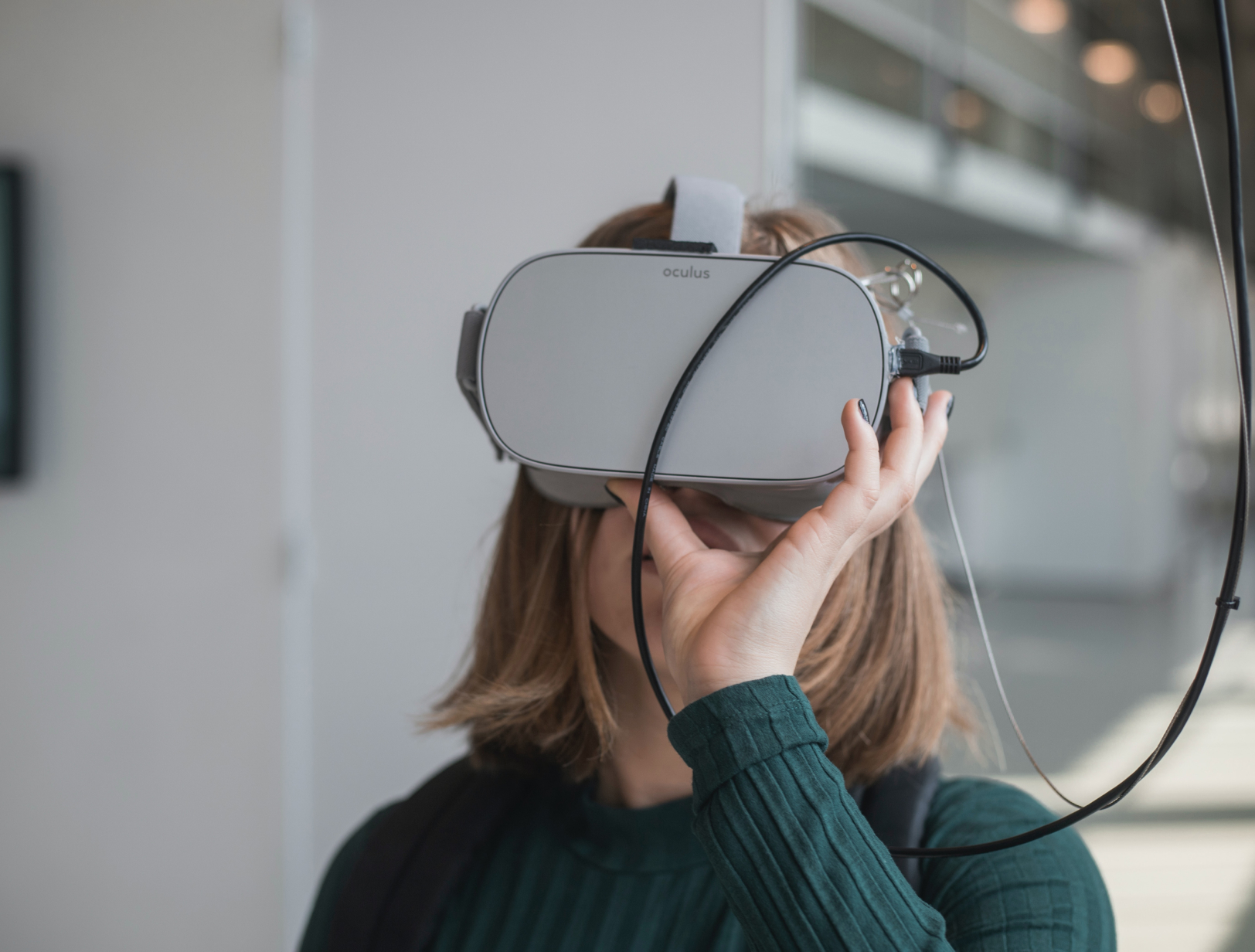
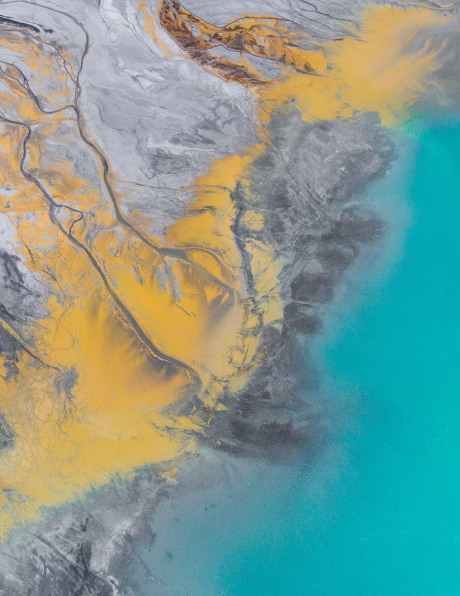
The end result
By maintaining an agile development process, we provided a high-quality solution tailored to RMC’s needs, improving data accuracy and worker adoption while gathering essential data for future AI training.
We did the first on-site tests for the full product in December. It is compatible with different bumper types and enables inspectors to log defects directly onto the model without leaving the inspection area. While inspectors still visually examine parts, the AR headset is expected to simplify defect logging, accelerating the inspection process and enhancing data accuracy. This step forward will strengthen RMC’s quality control and lay a solid foundation for training an AI model for automated defect detection in future iterations. RMC’s workers have responded enthusiastically to the AR headset, which integrates smoothly into their workflow.
What’s next
Future versions of the solution will involve training a machine learning model using data gathered from v1 of the solution and will ultimately introduce AI-driven defect detection through HoloLens 2. This model will enable real-time defect identification, leveraging computer vision to improve quality consistency.
The AR headset’s role will evolve to visualize defects detected by AI, making the inspector’s job even easier and further enhancing quality control. As AR and AI technologies gain traction in manufacturing, we’re excited to explore their potential not only for worker training but also to transform quality control, data collection, and analytics for small to mid-size manufacturers. By combining AR-based data collection with AI-driven insights, we’re ready to help RMC and other manufacturers unlock new possibilities in quality assurance, creating accessible, innovative solutions that drive efficiency and precision.
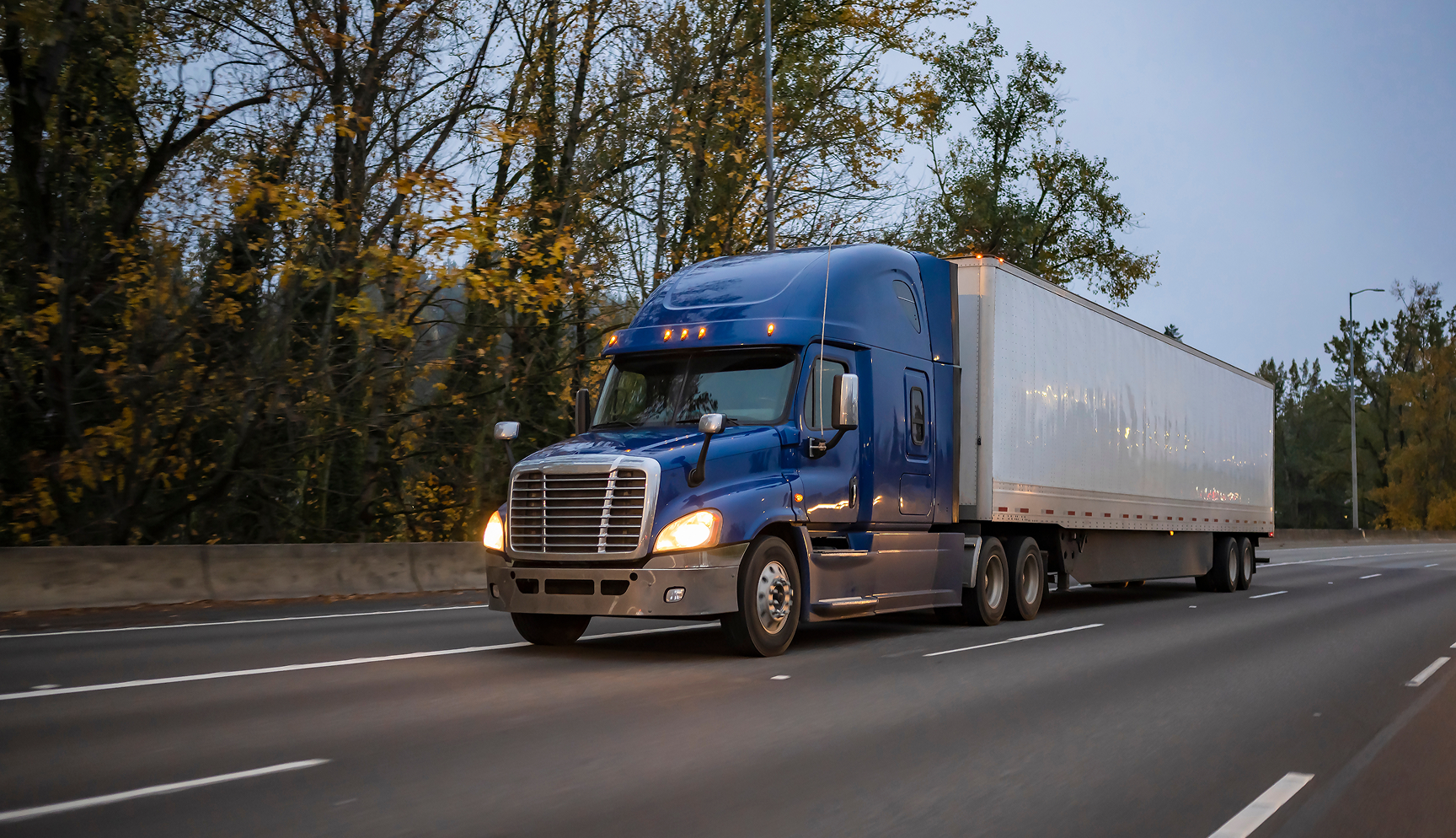
Did this project give you some ideas? We’d love to work with you! Get in touch and let’s discover what we can do together.
Insights
We’re on a constant quest to broaden our horizons and spread wisdom. It’s all about pushing boundaries and elevating our game.