Kruger
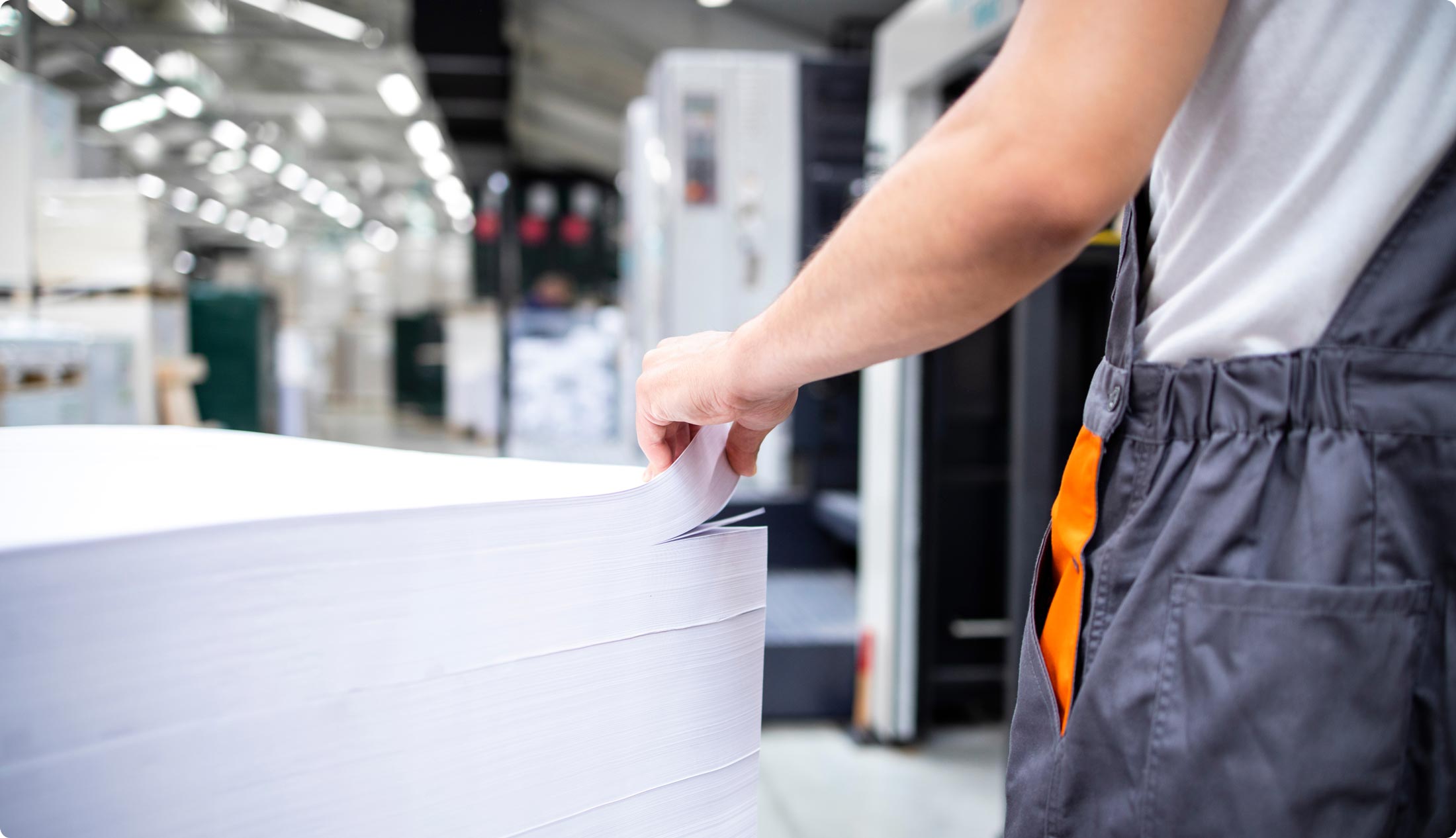
The context
In spring 2021, Osedea was selected as a partner for Scale AI’s largest-ever project, led by Canada’s leading tissue manufacturer Kruger Products. This multimillion-dollar undertaking was an investment at Kruger Products’ Sherbrooke plant to implement a digital twin of its supply chain. Following the grant, we were asked to develop an in-house software solution that would optimize the responsiveness and output quality of Kruger Products’ heavy machinery.
Project details
The challenge
Even the slightest misalignment of machinery can negatively impact an end product, not to mention it can give rise to pricey and time-consuming repairs. So, to ensure smooth operations and maintain Kruger Products’ excellent quality control, three lines of paper machinery need to be carefully monitored and maintained at the mill. Two key user types are responsible for overseeing this: operators (employees on the floor running the machines) and the performance team (a smaller seasoned group of machinery experts).
We were tasked with revamping Kruger Products’ existing solution called “Setpoint Tuning Tool.” The new visual interface would leverage data science and real-time data to show what was happening with each machine with high precision. The tool pulls and indicates ideal values from another tool where the performance team acts. Based on the displayed information, users can then optimize their reaction time and raise quality along the machinery through adjustments (e.g. correcting an out-of-centerline situation), and they can leave comments within the tool to justify any choice they make. As a new addition, we were asked to build in a troubleshooting guide that would assist operators when they encountered challenges with machinery.
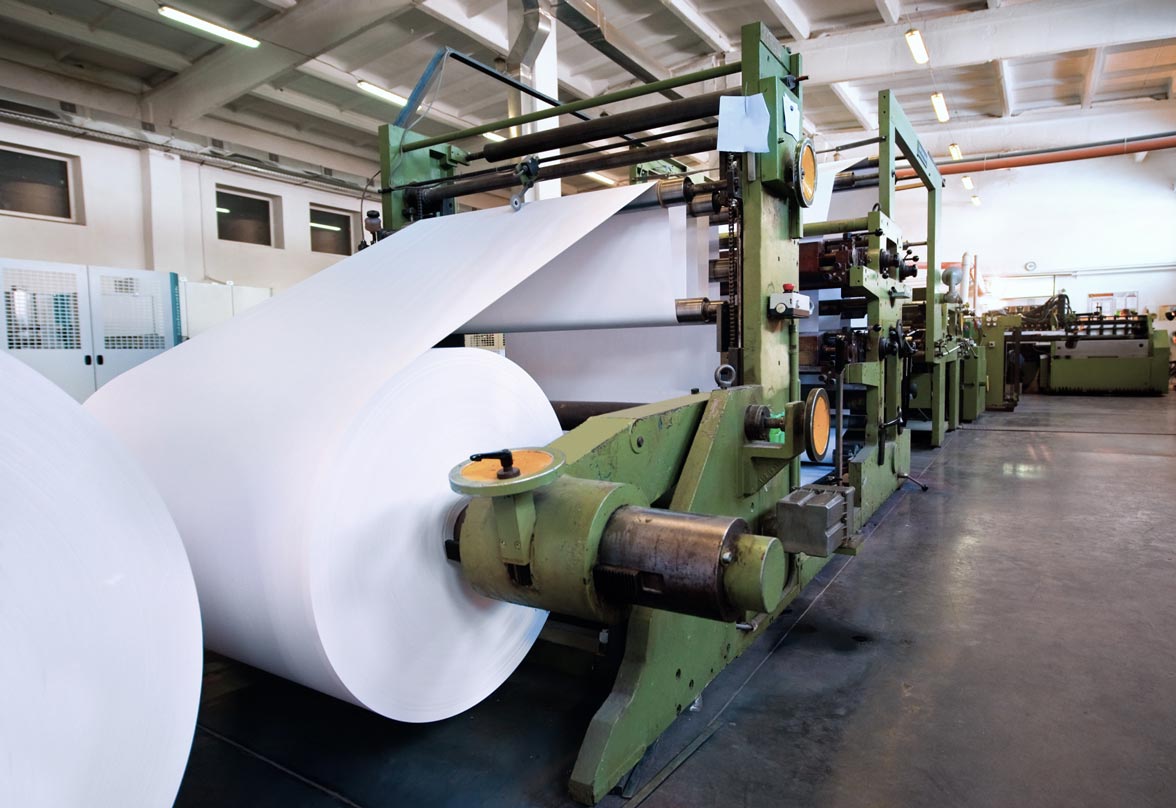
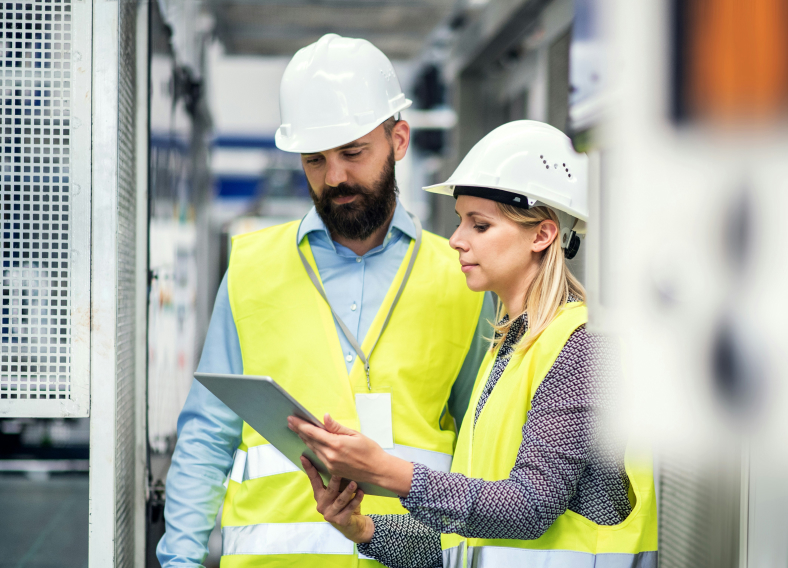
The task at hand
Even the slightest misalignment of machinery can negatively impact an end product, not to mention it can give rise to pricey and time-consuming repairs. So, to ensure smooth operations and maintain Kruger Products’ excellent quality control, three lines of paper machinery need to be carefully monitored and maintained at the mill. Two key user types are responsible for overseeing this: operators (employees on the floor running the machines) and the performance team (a smaller seasoned group of machinery experts).
We were tasked with revamping Kruger Products’ existing solution called “Setpoint Tuning Tool.” The new visual interface would leverage data science and real-time data to show what was happening with each machine with high precision. The tool pulls and indicates ideal values from another tool where the performance team acts. Based on the displayed information, users can then optimize their reaction time and raise quality along the machinery through adjustments (e.g. correcting an out-of-centerline situation), and they can leave comments within the tool to justify any choice they make. As a new addition, we were asked to build in a troubleshooting guide that would assist operators when they encountered challenges with machinery.
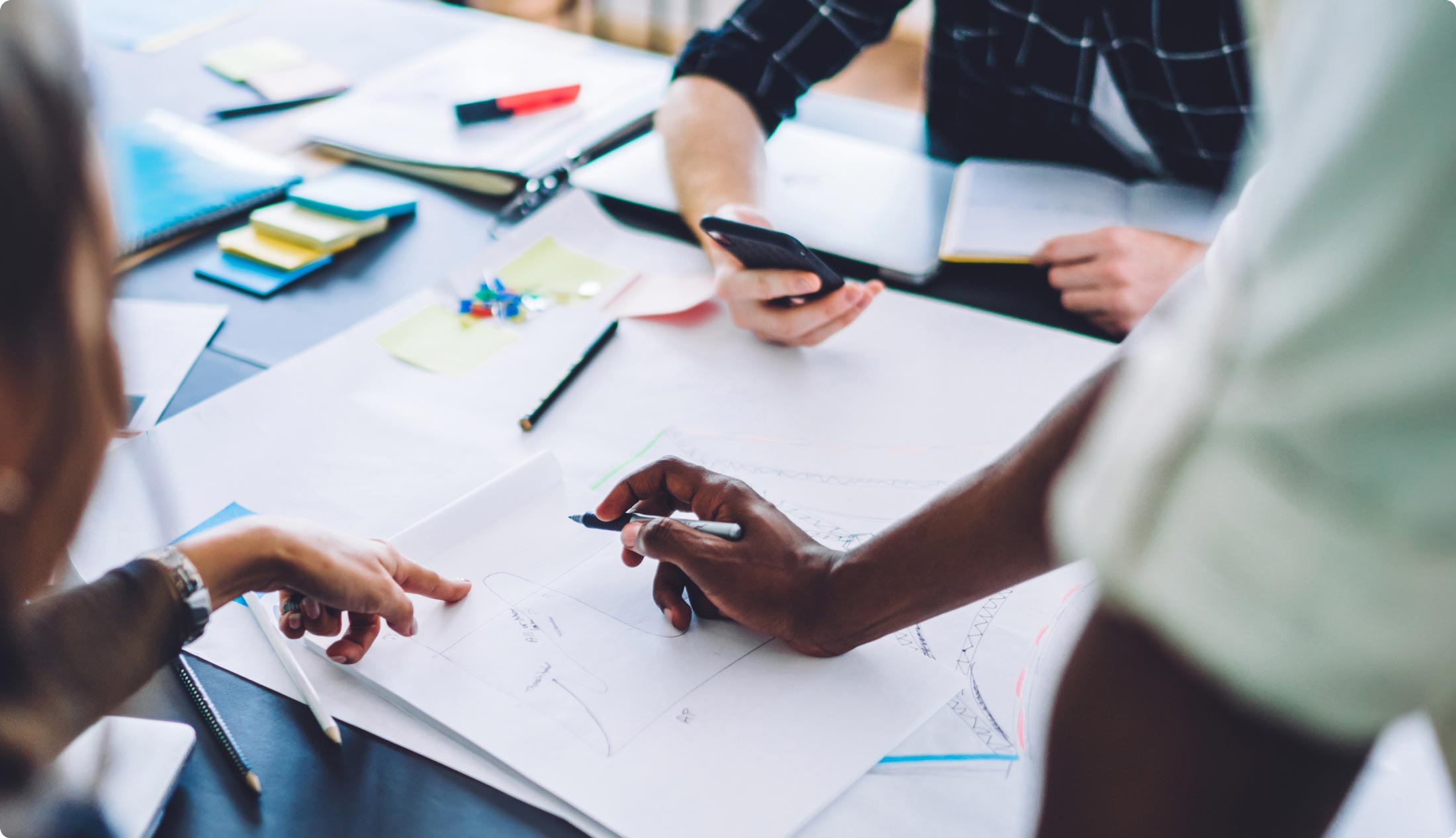
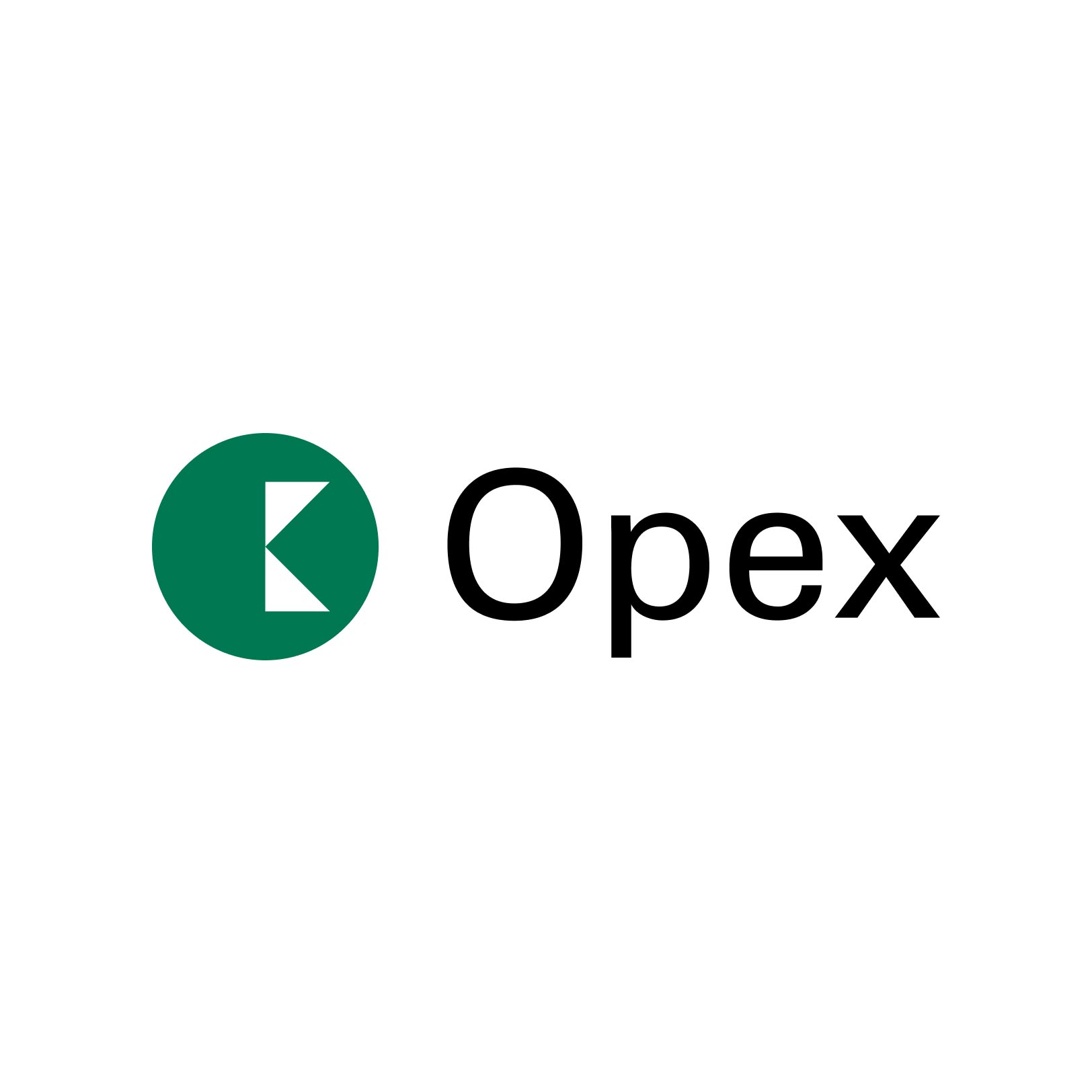
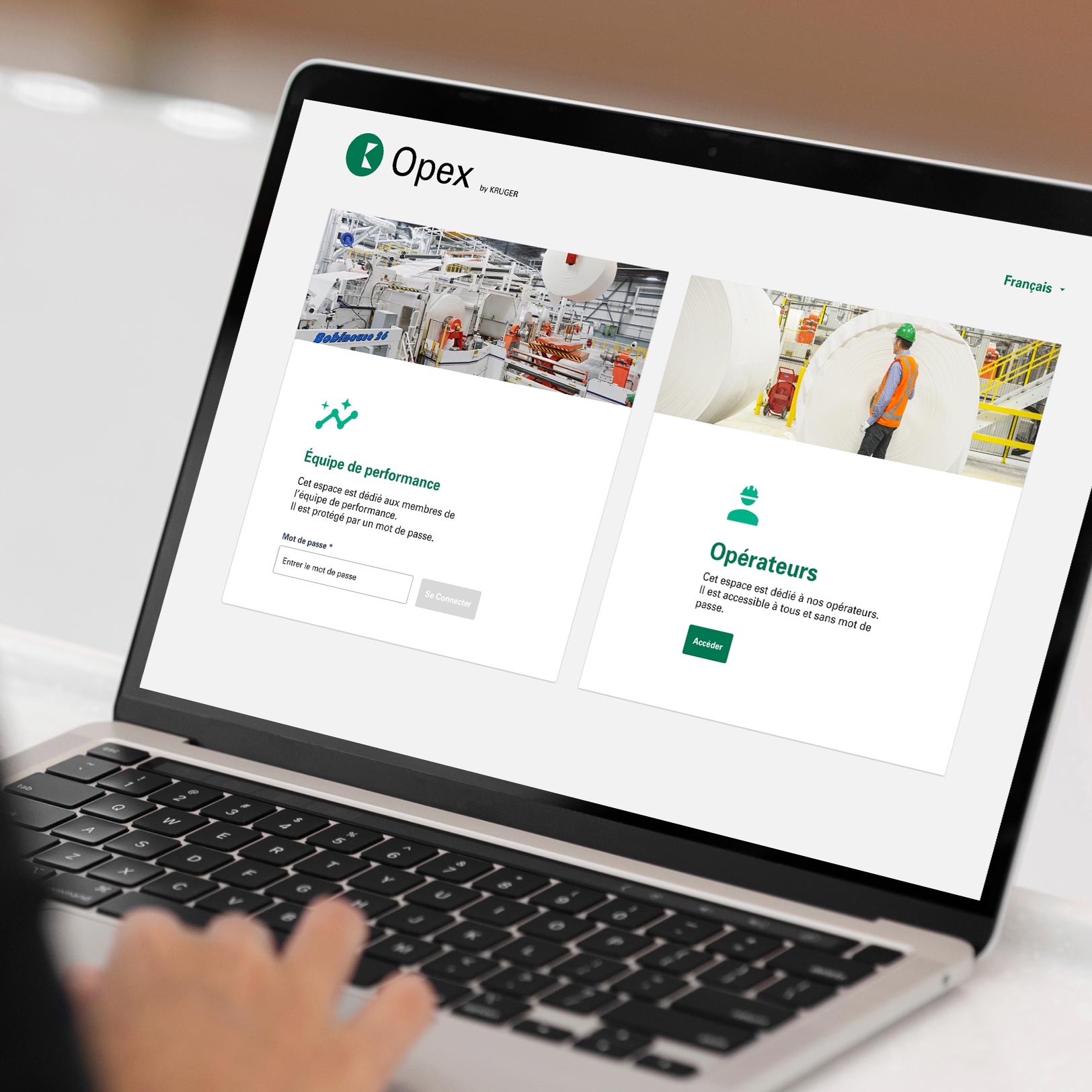
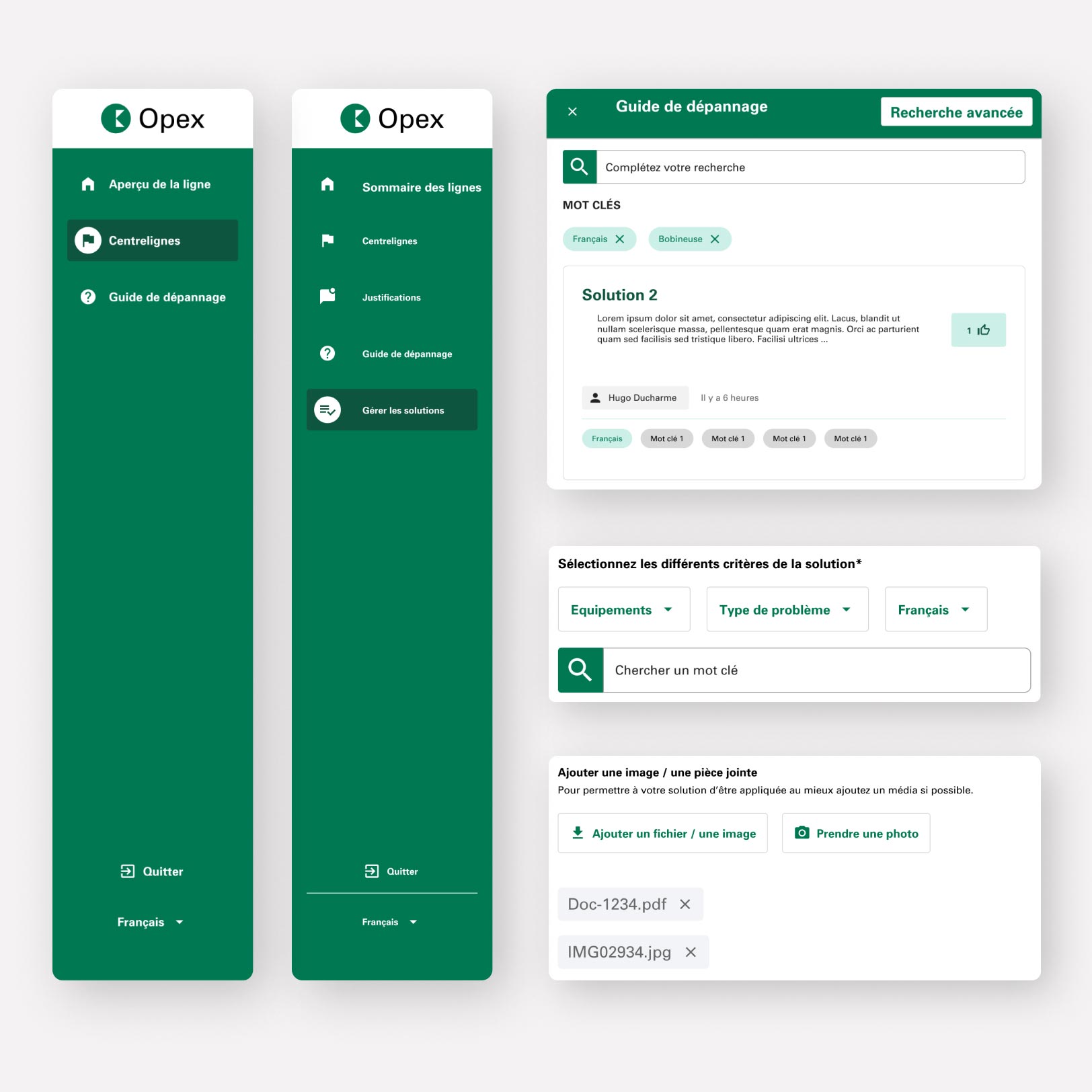
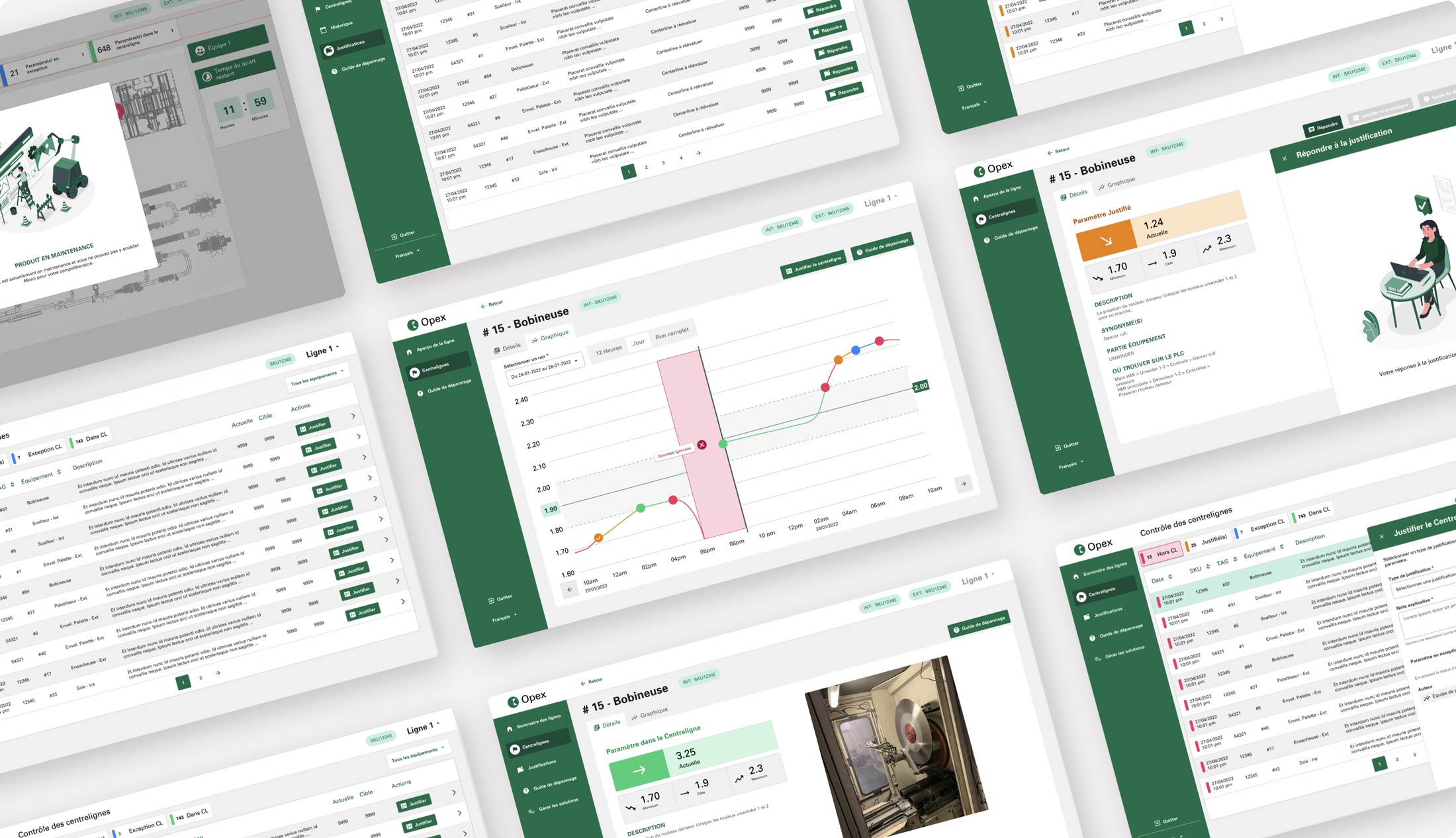
The end result
We were able to improve the performance and usability standards of the existing solution in the new version of Setpoint Tuning Tool. The finished solution offers a means of communication between the line operators and the performance team and includes key user-friendly features like the line interactive map available operators, a graph showing trends and tendencies of last runs, and justification trends and fluctuations, and also the introduction of the new "exception" status that allows a parameter centerline data to be ignored for a while. The built-in troubleshooting guide improves research efficiency by introducing tags on relevant keywords and becomes a participative tool by introducing a new moderation space.
The project involved a three-party relationship between us and BCG, the company who developed the back end. Working with multiple project leads was an interesting challenge for us, but we communicated well to hit our goals together.
What’s next
Setpoint Tuning Tool is currently in production at Kruger Products’ Sherbrooke plant and the company has plans to use it globally at their other mills starting sometime in 2023. Looking to the future, the company hopes the solution will reduce training time for new hires because it’s so intuitive. Additionally, there may be new opportunities to further manipulate the data, extend the graph functionality, and exceptions.
There were many knowledgeable people involved in this initiative and we’re very proud of the end result. For us, the project is testament to how our team members can handle highly technical projects, even in new-to-them industries. As we see it, thanks to our close relationships with our clients, we get to become experts at what they’re experts in. It excites us to get the chance to go beyond designing solutions that look good (though we do that too). We’re laser focused on usability, innovation, and bringing fresh ideas to the table.
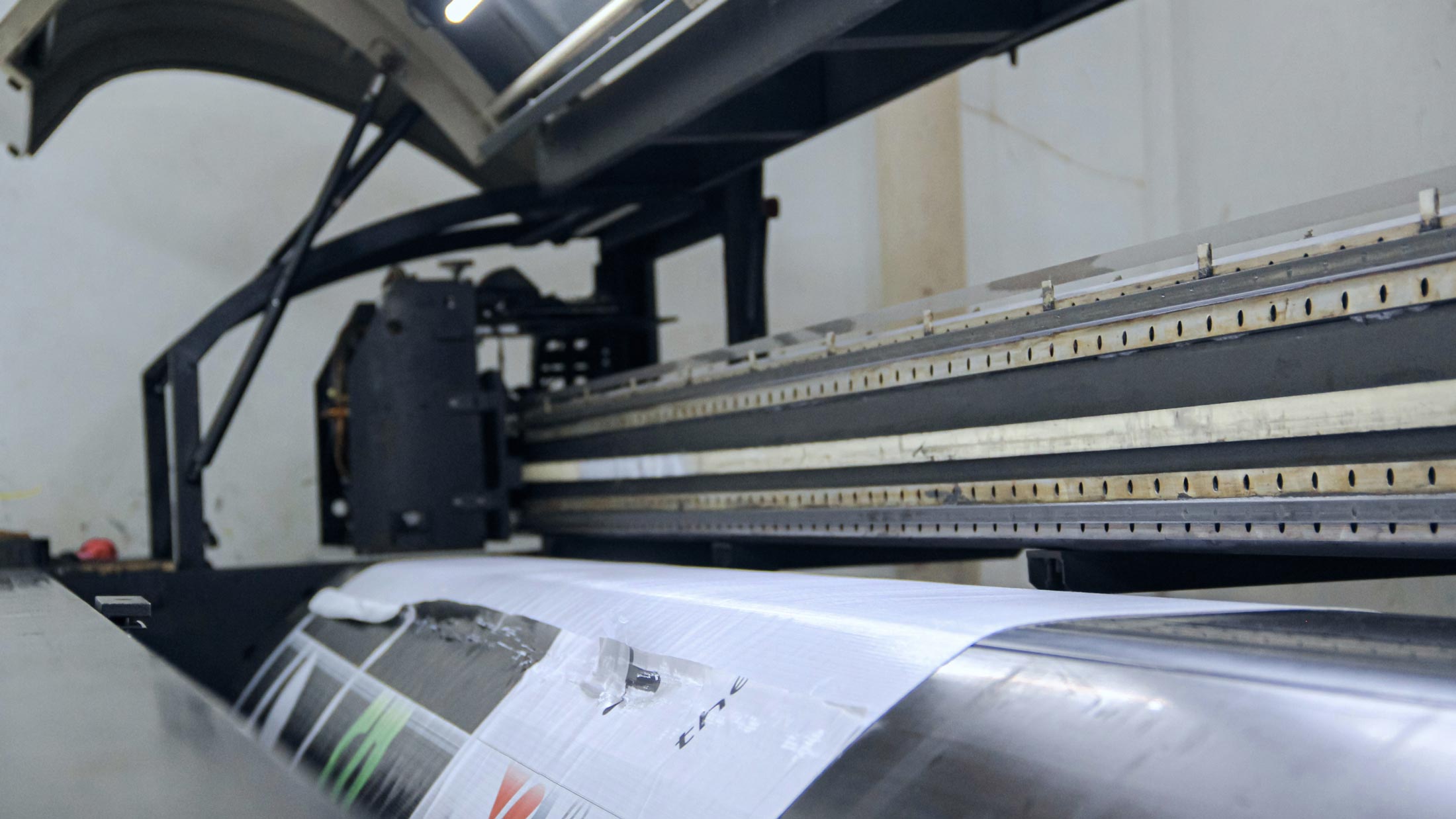
Did this project give you some ideas? We’d love to work with you! Get in touch and let’s discover what we can do together.
Insights
We’re on a constant quest to broaden our horizons and spread wisdom. It’s all about pushing boundaries and elevating our game.