Innovation
Driving innovation in aluminum smelting with Spot’s advanced tech
Osedea has been working closely with aluminum smelters in Quebec, to implement Boston Dynamics’ Spot robot into their workflows. This integration brings numerous benefits, including reducing human exposure to potentially hazardous environments—areas with high-voltage equipment, extreme temperatures, and poor air quality. In addition to safety improvements, Spot’s automated inspection capabilities provide consistent, accurate data that supports preventative and predictive maintenance strategies.
Confronting the challenge of electromagnetic interference
These smelting facilities generate strong electromagnetic fields in certain areas, especially near high-power equipment like transformers, rectifiers, and electrolysis cells. The magnetic field strengths in these areas often exceed 100 mG and can reach as high as 1,000 mG (1 Gauss). To put that in perspective, consumer electronics such as laptops and smartphones may experience temporary interference at around 100 mG, depending on their internal shielding. This interference presents significant challenges for tools and equipment, creating a clear case for implementing robots for teleoperation tasks and autonomous navigation.
Pushing Spot’s performance in tough conditions
Osedea stepped in to test how Spot could operate in these challenging environments. Our initial trials aimed to assess risk, feasibility, and potential return on investment for clients. Here’s a breakdown of what we learned from those trials.
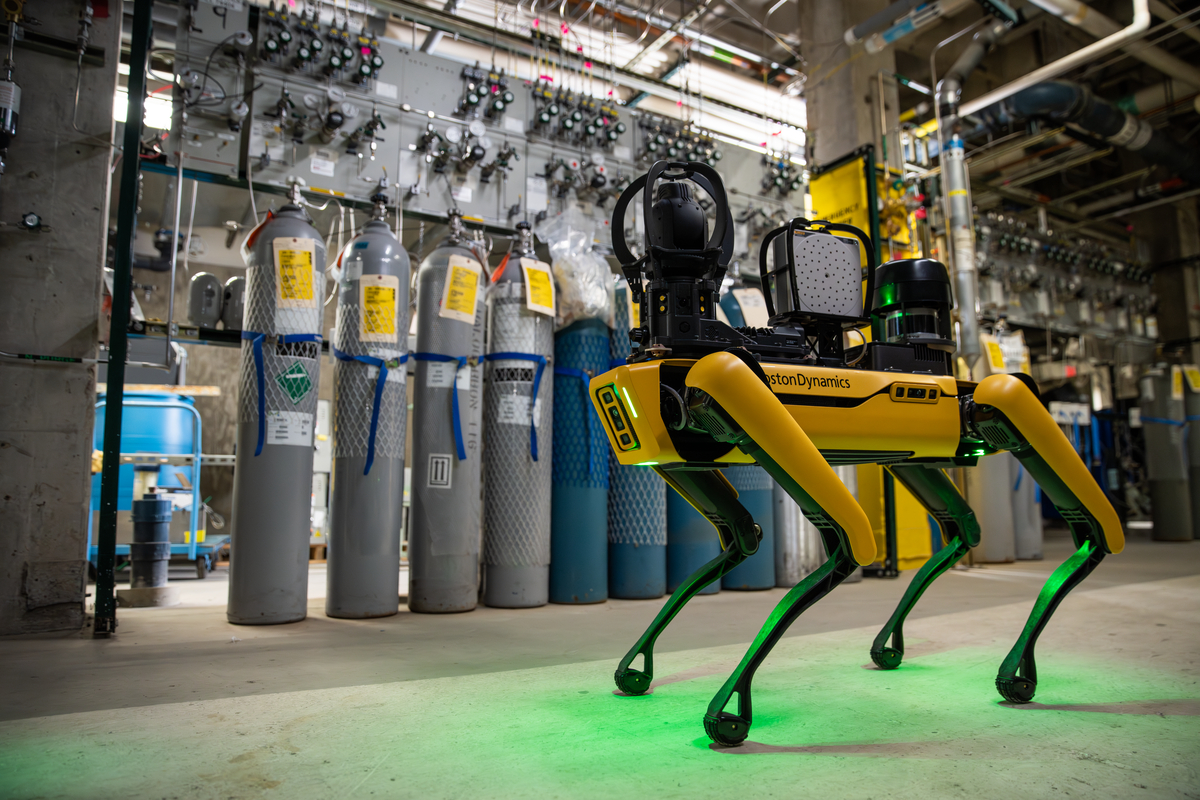
Testing beyond an arm’s reach
While we knew these environments weren’t exactly friendly to electronics, that didn’t stop us from pushing Spot’s limits. As an official Boston Dynamics’ business partner, our goal was to provide valuable feedback and unlock new ways to streamline our client’s workflows. We had confidence that Spot was the tool with the best potential.
For our first trial, we brought along our Explore Spot (legacy model), equipped with the Spot Arm, which enables physical interaction. While this configuration wasn’t ideal for autonomous inspection, it was the equipment we had available. As expected, Spot grabbed attention as it navigated along the dedicated walking path to the potroom, which houses the electrolytic cells (also called "pots") where the Hall-Héroult process takes place to produce aluminum.
As Spot entered the potroom, faults began to occur, causing Spot to sit in place—a safety feature Boston Dynamics built into Spot. This critical safety mechanism halts the robot when systems aren’t functioning properly, preventing any unintended actions or incidents.
After removing Spot from the area, it booted normally, leading us to deduce that the issue was with the Spot Arm, which lacks internal shielding (so it can stay effective and nimble). The arm’s motors couldn’t handle the higher electromagnetic interference, though Spot’s other systems were unaffected.
Continuing trials without the arm
For our second trial, Boston Dynamics loaned us a secondary Spot robot without the arm payload to further our testing. This time, our goal was to see if Spot could operate deeper within the strong electromagnetic fields. To our relief, Spot navigated the potroom successfully, proving that its internal motors and systems were resilient against electromagnetic interference—unlike the arm.
Enhancing Spot’s capabilities with advanced sensors
In subsequent trials, we were able to move on to the next unknown: payloads (i.e. additional sensors and hardware to expand Spot’s functionality) and their resistance to electromagnetic interference.
We equipped Spot with Boston Dynamics’ Enterprise Asset Management (EAM) kit for automated inspection. This kit includes the Spot CAM+IR, a powerful multi-camera system which captures RBG and thermal images, the Fluke SV600 acoustic imager (to locate and visualize air and gas leaks or changes in sound signatures before they become costly problems), and the Spot EAP2, which enhances the autonomy, computation, and communications available on the Spot platform.
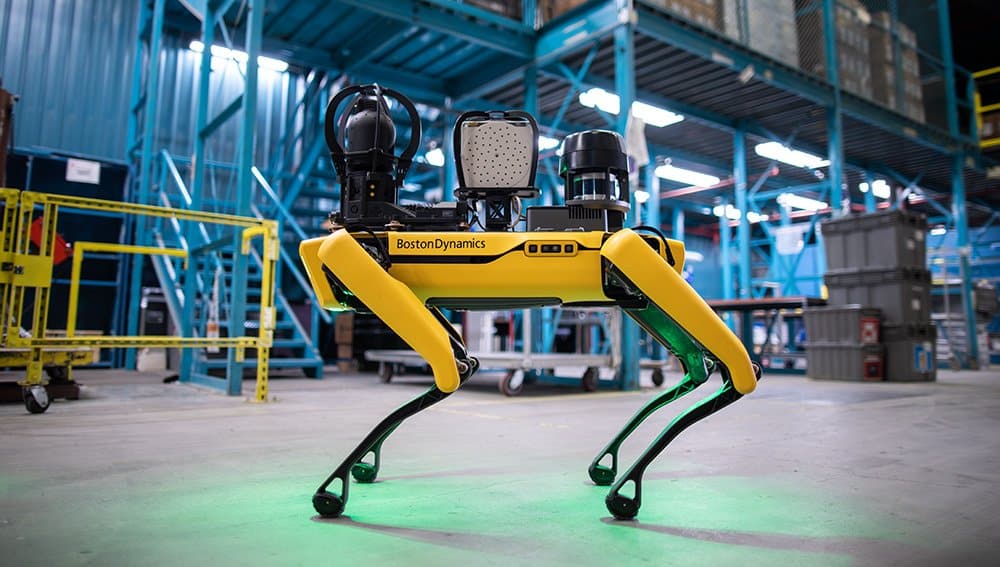
However, in other high-level zones, deep into the electromagnetic fields, Spot exhibited strange behaviour when standing still—Spot would “dance” on its own, stepping or rotating to self-balance. We suspect the magnetic fields were causing slight interference with its balance systems, which Spot was compensating for.
Exploring what’s next for Spot deployment
It’s clear that Spot has enormous potential for aluminum smelting environments, especially where human safety is at risk. At Osedea, we’re committed to pushing the boundaries of what robotics can do, especially in tough conditions like these. Automating tasks in hazardous environments is key to improving safety and efficiency.
Further trials are necessary to fully understand how electromagnetic interference affects Spot and its various payloads. With the right onboard sensors and plotting software, we can aim to automate 80% or more of a facility’s inspections—cutting downtime and boosting productivity.
Ready to integrate Spot into your operations?
Boston Dynamics has built a robust dynamic sensing platform with Spot, and though it has its limits, continued testing in extreme environments will reveal even more of its potential. These automation tools are essential not only for cost savings but also for the safety of your personnel.
Osedea offers proof of concept trials—whether in challenging environments like aluminum smelters or more routine manufacturing settings. Send us a message, we’d love to discuss how we can collaborate and explore how Spot could enhance your operations!
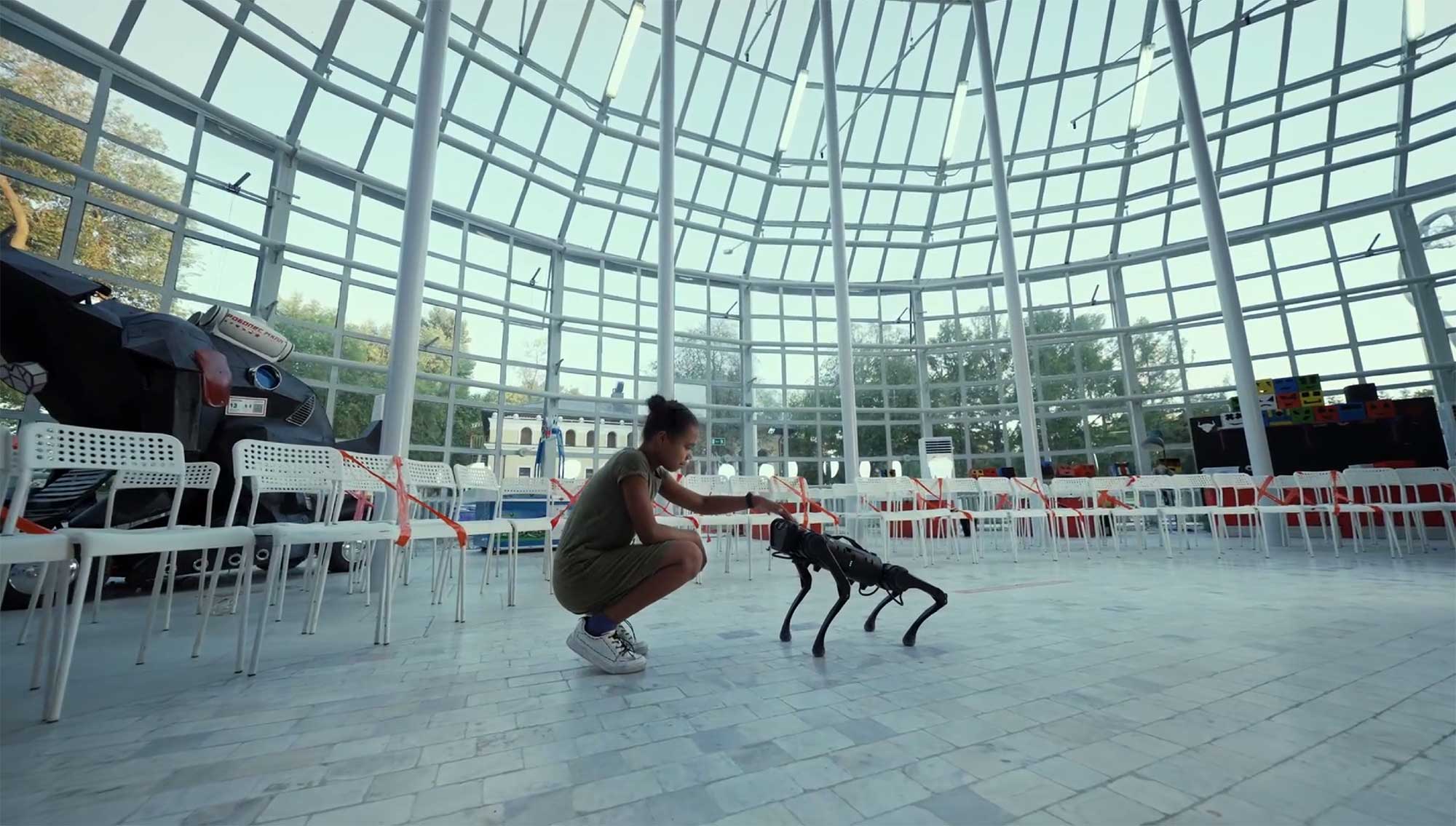
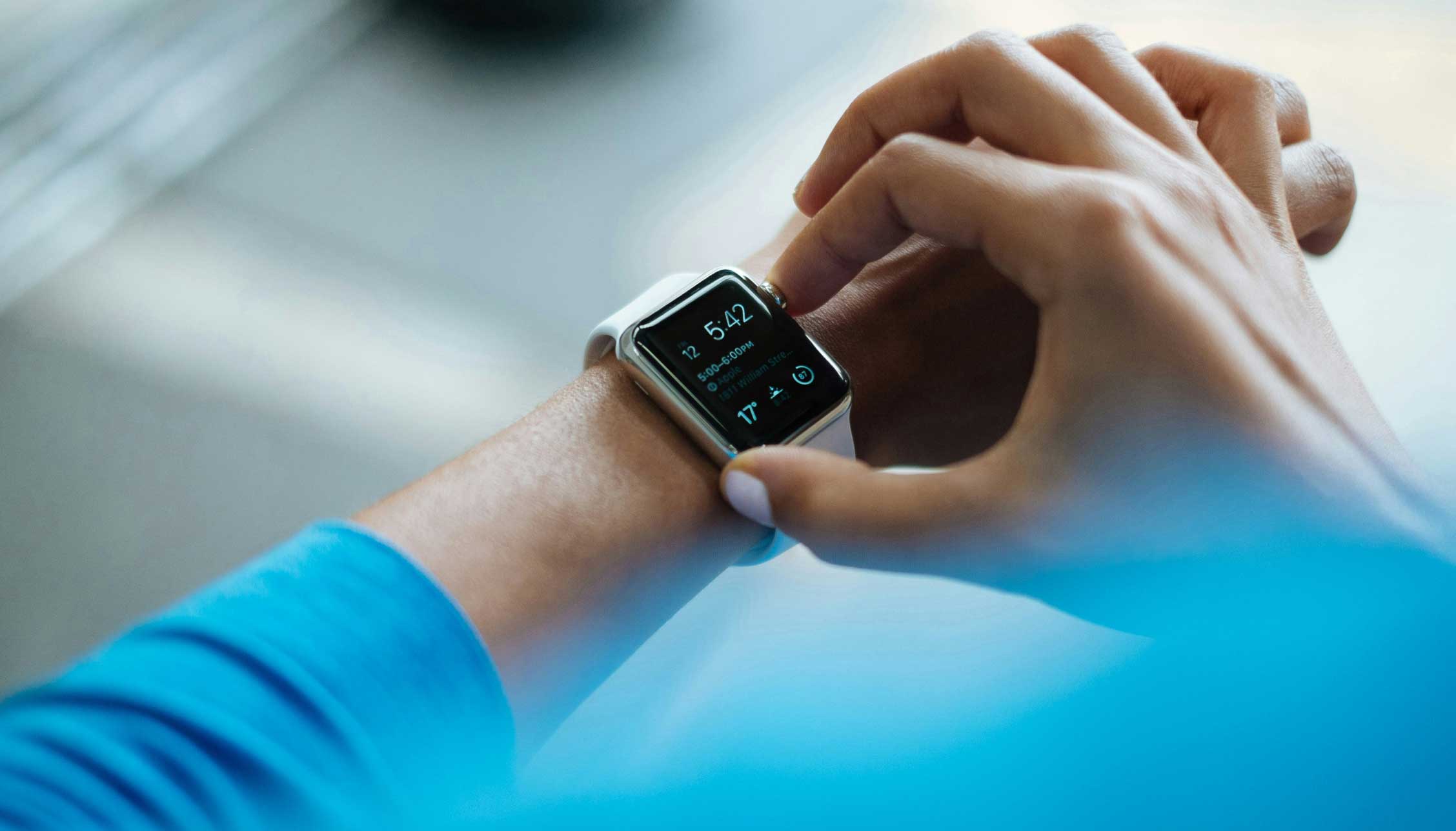
Did this article start to give you some ideas? We’d love to work with you! Get in touch and let’s discover what we can do together.