Innovation
Revolutionizing metallurgy: AI and nanotech in metal extraction
The way we extract, process, and separate materials is about to be disrupted—again. After attending the 63rd Annual Conference of Metallurgists, it’s clear: the future of metallurgy is taking shape at the intersection of AI, biology, and advanced manufacturing. These disciplines are converging to transform what’s possible—from nanoscale material separation to smart, scalable extraction systems.
At Osedea, we’re always exploring what’s next in tech—especially when it connects to industries we support, like mining and metallurgy. Here’s a look at some of the most exciting ideas reshaping the field.
A wealth of data to leverage
We’ve built an incredibly diverse knowledge base of various nanotechnologies. PubChem contains 111 million unique chemical structures, most of which are either human-made or natural. Artificial intelligence has predicted the structure of 200 million proteins. A substantial database of 500,000 proteins in bacteria has been identified to be directly linked to atomic/molecular separation and transport. The pieces are falling into place to tackle some of humanity’s biggest challenges, like efficiently extracting metals.
Rethinking metal separation
One such classic challenge is the separation of particles from each other. At the base of the supply chain is the processing of ore by milling it, separating the precious metal, and purifying it. Solvent Extraction (SX) is a key technique, refining copper from low concentrations (2 g/L) to 99% purity copper plates. At the core of this process are molecules that bind to metal ions. The molecules are organic (oil-like) and therefore float when in aqueous solution. The organic phase is then transported to another aqueous solution where the ions are released. The pH of the aqueous solution controls whether the molecule binds to a metal ion, or whether it releases it.
Hundreds of molecules have been chemically engineered to perform solvent extraction. One such molecule is the CYANEX reagent (C₁₆H₃₅O₂P). It has high selectivity for cobalt (Co) or nickel (Ni). The metal ion will bind to the top oxygen (red) atom. More on this molecule in this article.
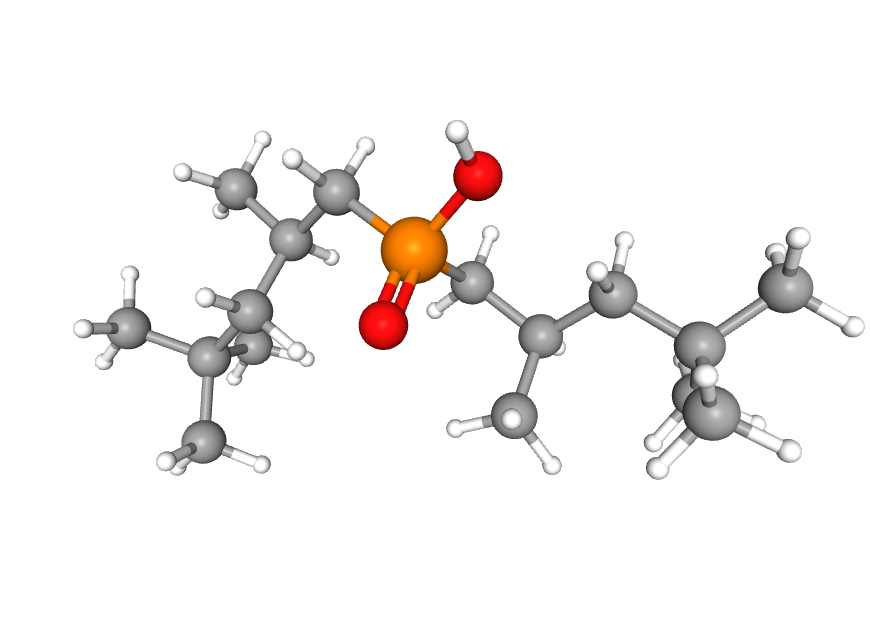
But chemical engineers aren't the only ones with sophisticated molecules capable of isolating metal ions. Nature has been ahead of us for millions of years. To maintain homeostasis, bacteria must consume material from their environment, transport ions to specific locations within their cells, and process them. Scientists have cataloged half a million genes and proteins that manage atomic-level interactions, offering a blueprint for advanced separation techniques.
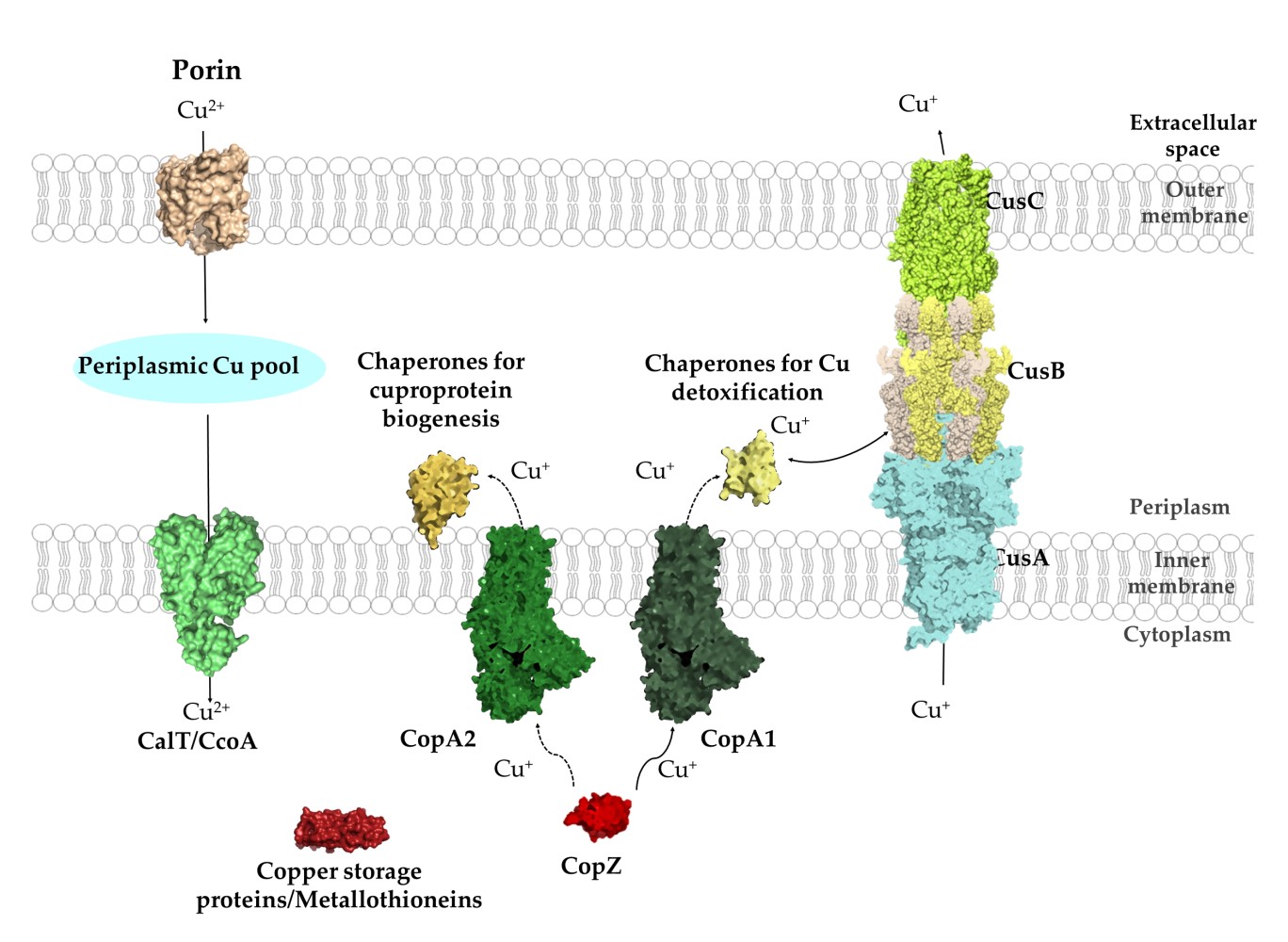
The key difference between an ACORGA molecule and a bacterium is their size. The ACORGA molecule is ~2 nanometers. The Porin transmembrane protein shown above is ~1.7–3 nanometers. Comparing that to the ~1 micrometer of the average bacterium—three orders of magnitude bigger!
Scaling up: from molecules to structures
Nanotechnology engineers are pushing boundaries with additive manufacturing. The engineers presented their study where they created a 3D cube, with struts 50 micrometers in diameter (recall that a bacterium is ~1 micrometer in size). Within the cube, the engineers layered in plates 2 mm thick. The goal of their study was to compress the cube and evaluate the compression strength of the lattice. At these scales, a single strut is about the size of a eukaryotic cell. For comparison, the cytoskeleton’s microtubules (biological struts) are ~25 nanometers in diameter. The main idea to recognize though is the scale at which these structures can now be printed “cheaply.”
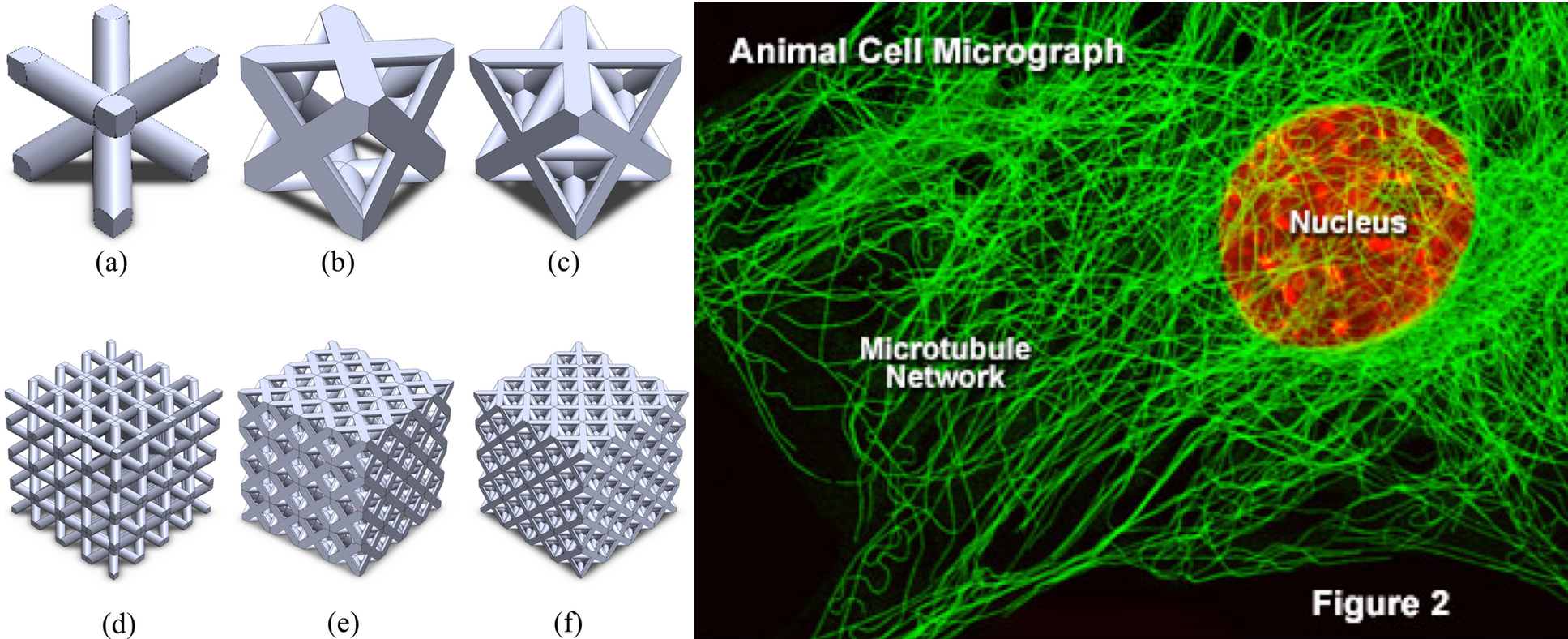
Another talk in additive manufacturing focused on the introduction of “defects” in hexagonal structures. Bees naturally construct honeycombs with hexagonal variations to create specific shapes, either concave or convex, especially at the periphery or on curved surfaces. Researchers from the University of Victoria introduced these defects in a 3D printed honeycomb lattice cube. They demonstrated that the shape and position of the defects had a direct effect on where and how the material deformed when stresses induced mechanical failures.
Failure isn’t just a macro-scale concern (think hydrodam collapses)—it happens at the nanoscale too. The key is designing materials that fail in predictable, controlled ways, reducing risk and improving safety. Self-healing and adaptive materials are already under development, bringing us closer to this goal.
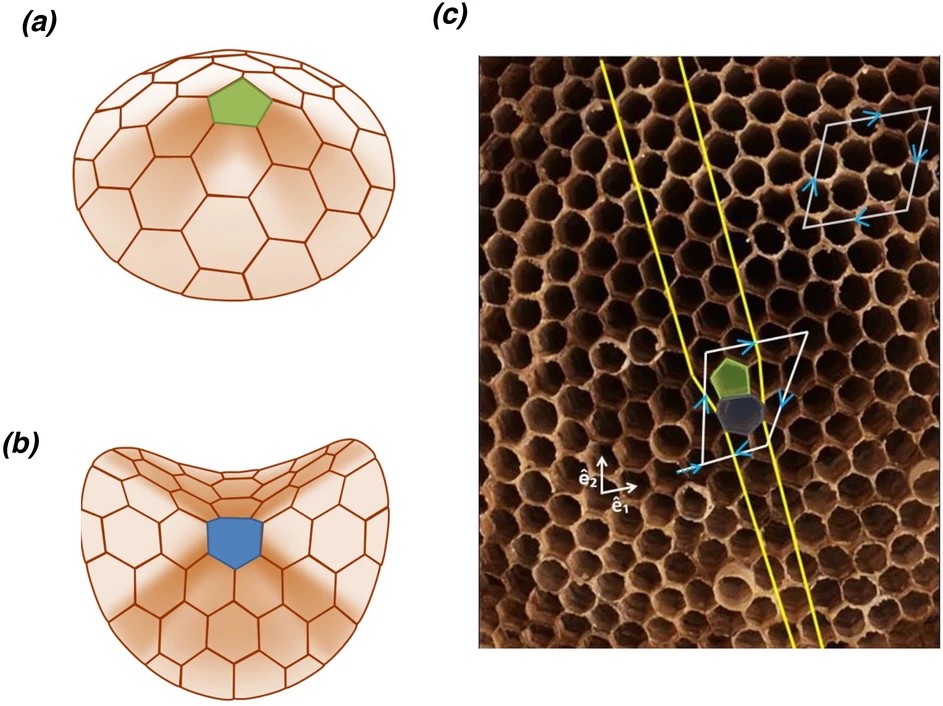
Engineering the building blocks
To make the material used for additive manufacturing, spherical-shaped pebbles are typically used. A researcher from the University of Alberta presented at the conference an alternative to traditional gas atomization. The team used an induction coil and a vibrating metal plate to create 100-micrometer metal spheres. By controlling the oscillation frequency, researchers could fine-tune the droplet formation process. As the ripples formed, crests would develop, releasing blobs of molten metal that naturally formed spheres due to surface tension. This technology offers great precision in producing uniform metal powders.
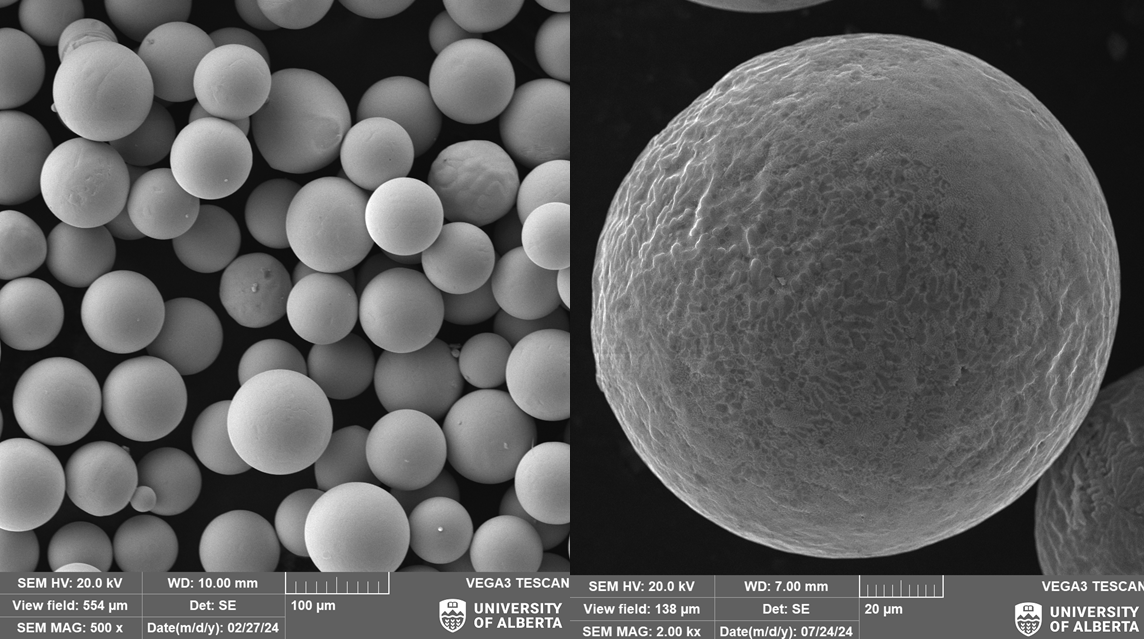
The bigger picture
We usually build mines around high-concentration ores, extracting one or two valuable metals while discarding the rest. SX plants process huge volumes of dissolved minerals, with the goal of isolating just one. What happens to the other 117 elements? They’re lost to waste, known as “tailings”.
Now, imagine a compartmentalized, scalable system—a network of micron-scale chambers, each optimized for a specific task. Some isolate elements using ACORGA-like molecules, others break down compounds with bacteria, and some regulate acidity or store extracted materials. Each chamber functions like a specialized cell, working together to separate every valuable element. The potential for cross-industry applications is massive, from mining to waste processing and e-recycling. Achieving this level of modularity and scalability would revolutionize resource separation.
Achieving reusability across industries and use cases is the only way to achieve the economies of scale necessary to make such a design effective. With a catalogue of thousands of specialized cells, we can build interconnected networks for any given use case. Solvent extraction may require more cells with a specialized molecule, whilst trash disposal may require more bacteria colony cells, but they both require air and liquid distribution channels (among other common structures).
It’s worth noting that several projects of this sort are already underway. One can think of the Syensqo Cube, an auto-dosing system for flotation-based separation. Microfluidic separation systems are also common amongst researchers for continuous flow separation. The separation of rare earth elements typically involves 50+ stages—a network of 50 car-sized compartments.
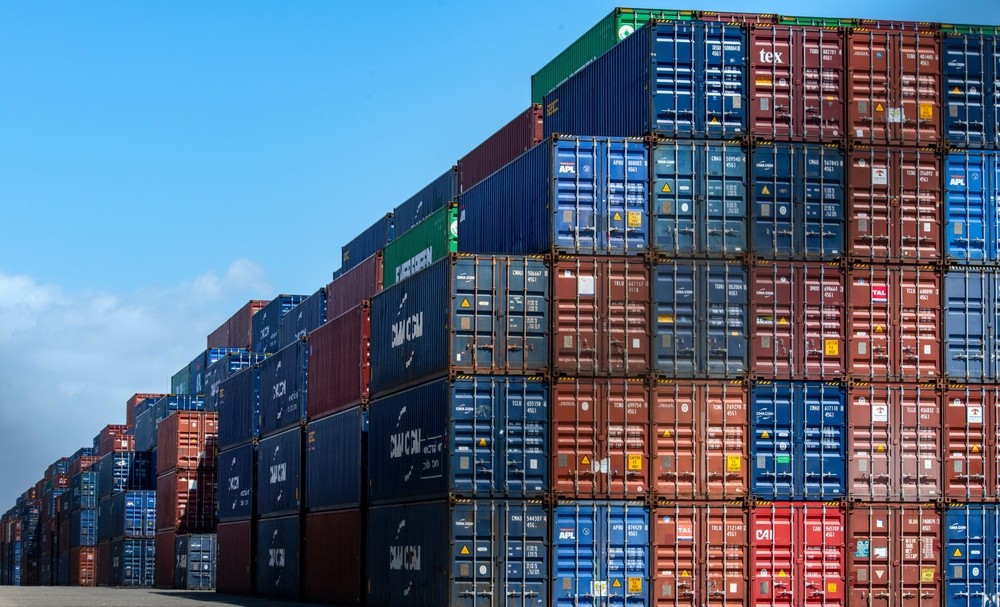
Breaking the silos
One of the biggest challenges in metallurgy—and science as a whole—is siloed thinking. Industries, research fields, and institutions often operate in isolation, limiting progress. But breakthroughs happen at the intersections of disciplines. Metallurgy isn’t just about chemistry or engineering anymore. It’s about biology, AI, and advanced manufacturing working together.
What's next
The conversations are just getting started. The cross-pollination of biology, AI, and advanced manufacturing is unlocking entirely new ways to approach challenges like metal separation, resource recovery, and scalable, adaptive systems. At Osedea, we’re already helping clients in mining and industrial sectors turn complexity into opportunity—through smart software, automation, and cutting-edge innovation. Let’s talk about building what’s next.
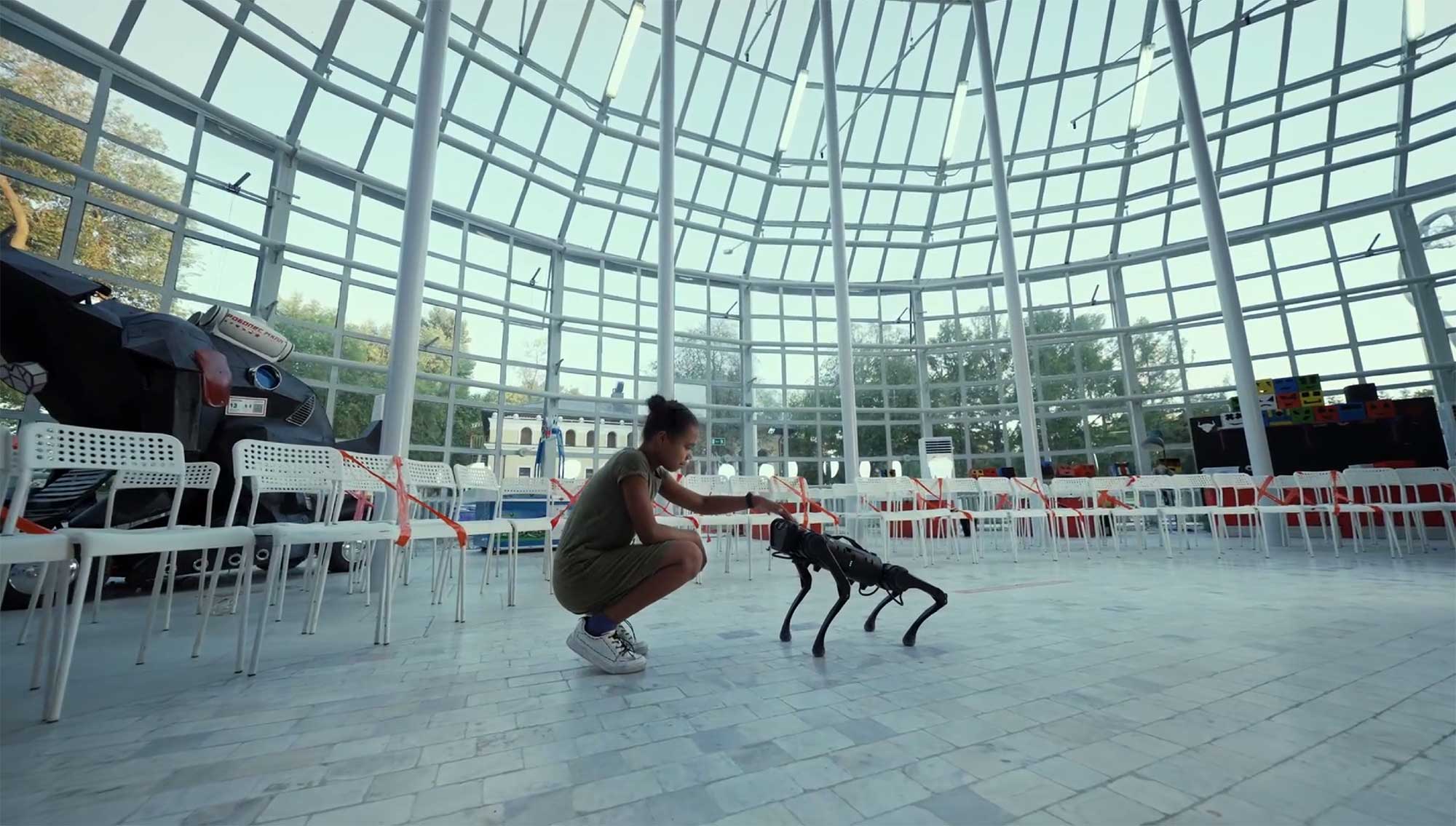
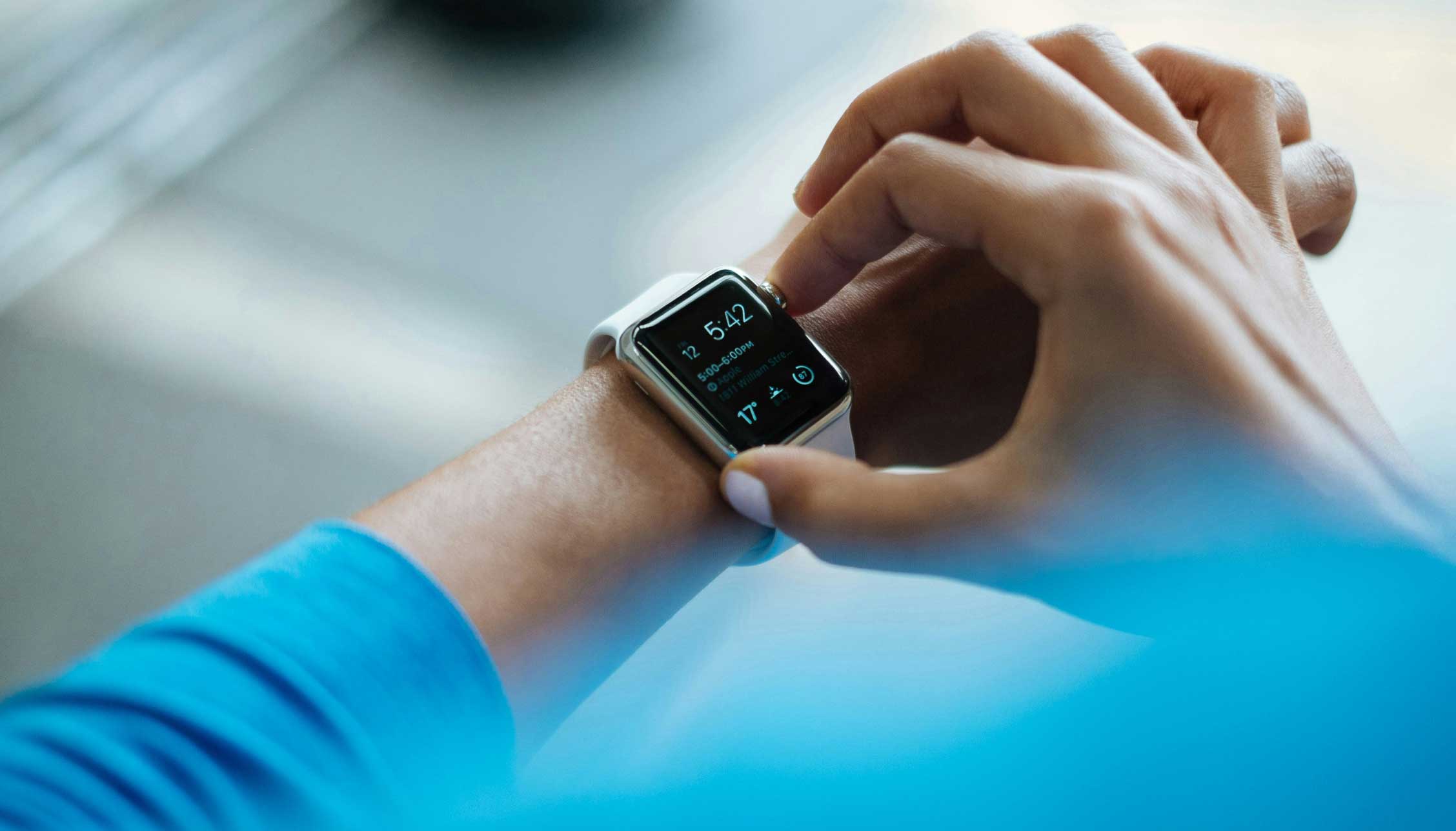
Did this article start to give you some ideas? We’d love to work with you! Get in touch and let’s discover what we can do together.