Innovation
Enhancing mine safety and efficiency with Spot and LiDAR
We are currently collaborating with a mining company to explore innovative solutions for enhancing their operations’ efficiency. One of the significant challenges they face is the post-blast inspection process. Their current method is both risky and inefficient: they use an excavator equipped with a scanner attached to its bucket, which is remotely controlled to perform the scan. This approach not only poses safety risks but also carries the potential for environmental and equipment damage. Moreover, while the excavator is occupied with scanning, it is not engaged in ore collection, which leads to substantial cost implications. This is where our idea of leveraging Boston Dynamics’ Spot robot in combination with the Emesent Hovermap ST-X comes into play.
A bit of background
The mining industry, one of the oldest in human history, has gradually adopted new technologies to increase efficiency and reduce environmental impact. Today, in a world of automation, platforms like Boston Dynamics’ Spot can significantly contribute to this evolution. These robotic implementations not only enhance operational efficiency but also remove humans from unsafe environments, or at the very least, reduce their exposure, allowing them to focus on more innovative tasks.
In this article, we will primarily explore the impact of 3D mapping using LiDAR within mines. However, it’s important to note that Spot has multiple use cases in the mining industry, thanks to its mobility, agility, and advanced sensing capabilities.
What is the Hovermap ST-X?
The Hovermap ST-X takes SLAM-based LiDAR mapping to new heights and enables autonomous mapping of large assets and complex terrains.
LiDAR (Light Detection and Ranging) is a sensing technology that uses laser light to measure distances and create precise, three-dimensional maps of the environment. It operates by emitting laser pulses and measuring the time it takes for the reflections to return, allowing for accurate distance measurements to various objects and surfaces. The Hovermap ST-X enhances the capabilities with a vertically mounted LiDAR puck that rotates during scanning, providing a broader field of view. With a sensing range of 300 meters and the ability to capture over a million points per second, it gathers detailed, accurate data for a wide range of applications.
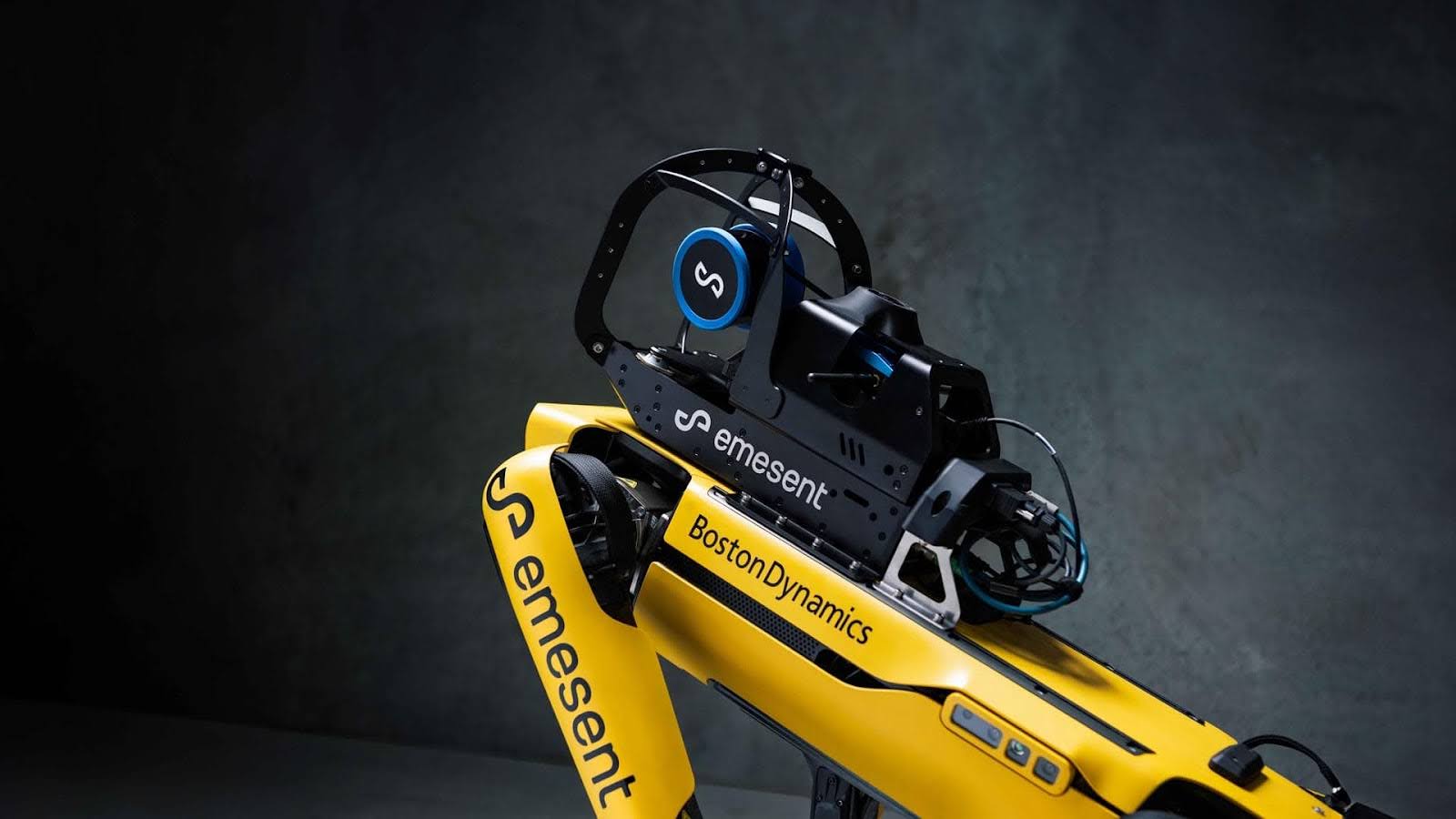
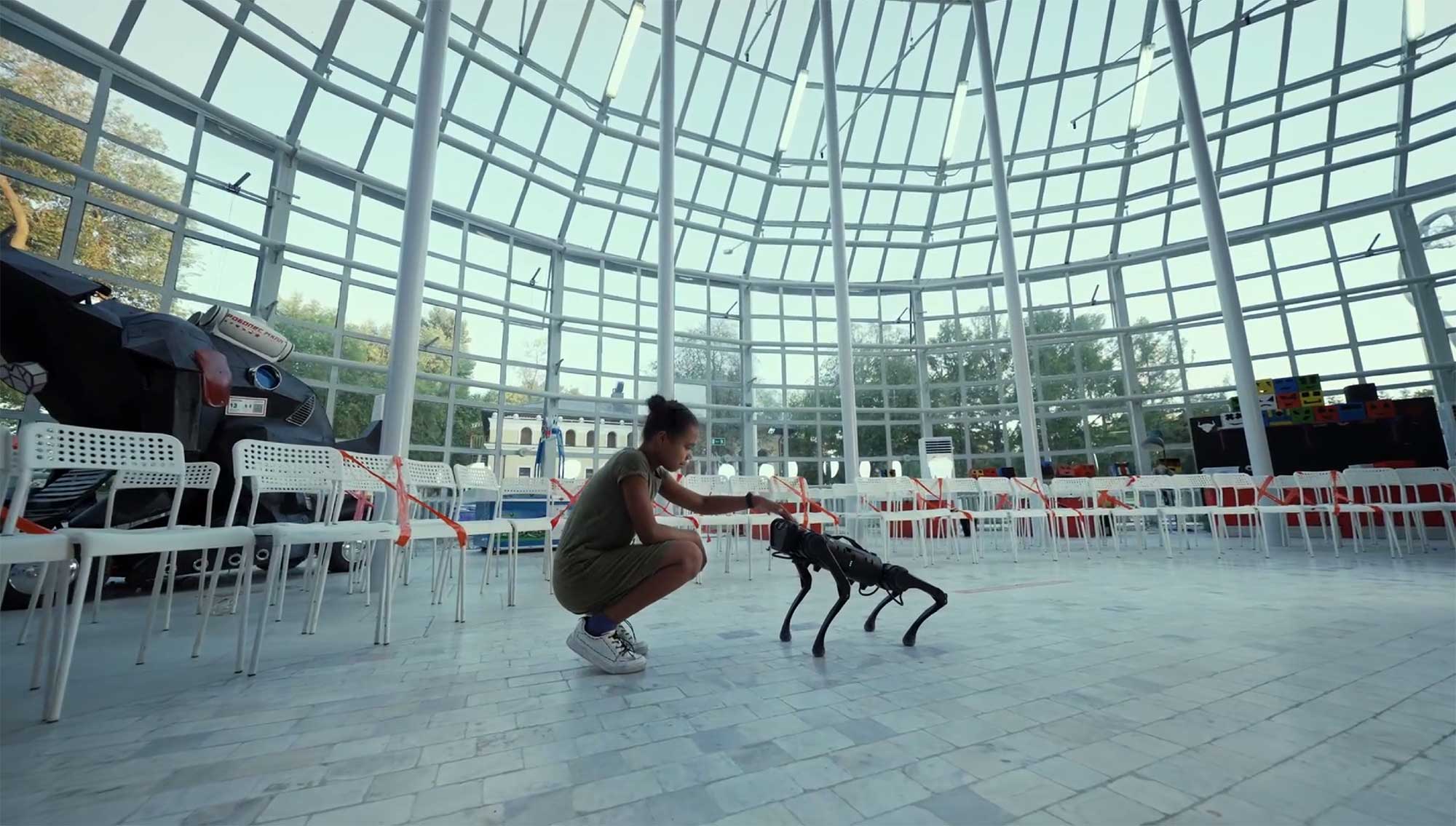
While our focus is on the synergy between Spot and the Hovermap ST-X, it’s worth noting that the Hovermap ST-X is versatile enough to be handheld or mounted on various vehicles, including drones. Read more about Hovermap ST-X on the Emesent website.
Why is 3D mapping crucial in the mining industry?
3D mapping of underground mines is vital for optimizing mine development and operations. It enables more informed decision-making, such as data-driven decisions about previously unexplored or inaccessible areas such as stopes, ore passes, and vent raises. Additionally, it improves safety by eliminating the need for personnel to enter hazardous areas to collect data. The technology also ensures certainty and cost savings by reducing the time required to scan drifts, stopes, and raises, thereby making the process more efficient. Furthermore, it can reduce reliance on costly equipment and consultancy services that would otherwise be needed.
Spot and the Hovermap ST-X combined
Deploying Boston Dynamics’ Spot robot with the Hovermap ST-X offers significant cost reductions and enhances safety for personnel. Instead of diverting resources to perform manual scans or relying on riskier methods, Spot can be utilized to remotely and safely mobilize LiDAR technology. An operator simply needs to bring Spot to the area of interest, boot it up, and guide it into restricted areas. The Hovermap ST-X’s ability to capture large amounts of data quickly and across a broad range makes this a simple in-and-out procedure for Spot.
Alternatively, Spot can operate autonomously using various methods, such as Autowalk Missions or custom commands via the Spot SDK. Imagine Spot booting up in your cargo van, walking out on its own, performing the scan, and returning—all without requiring any manual intervention.
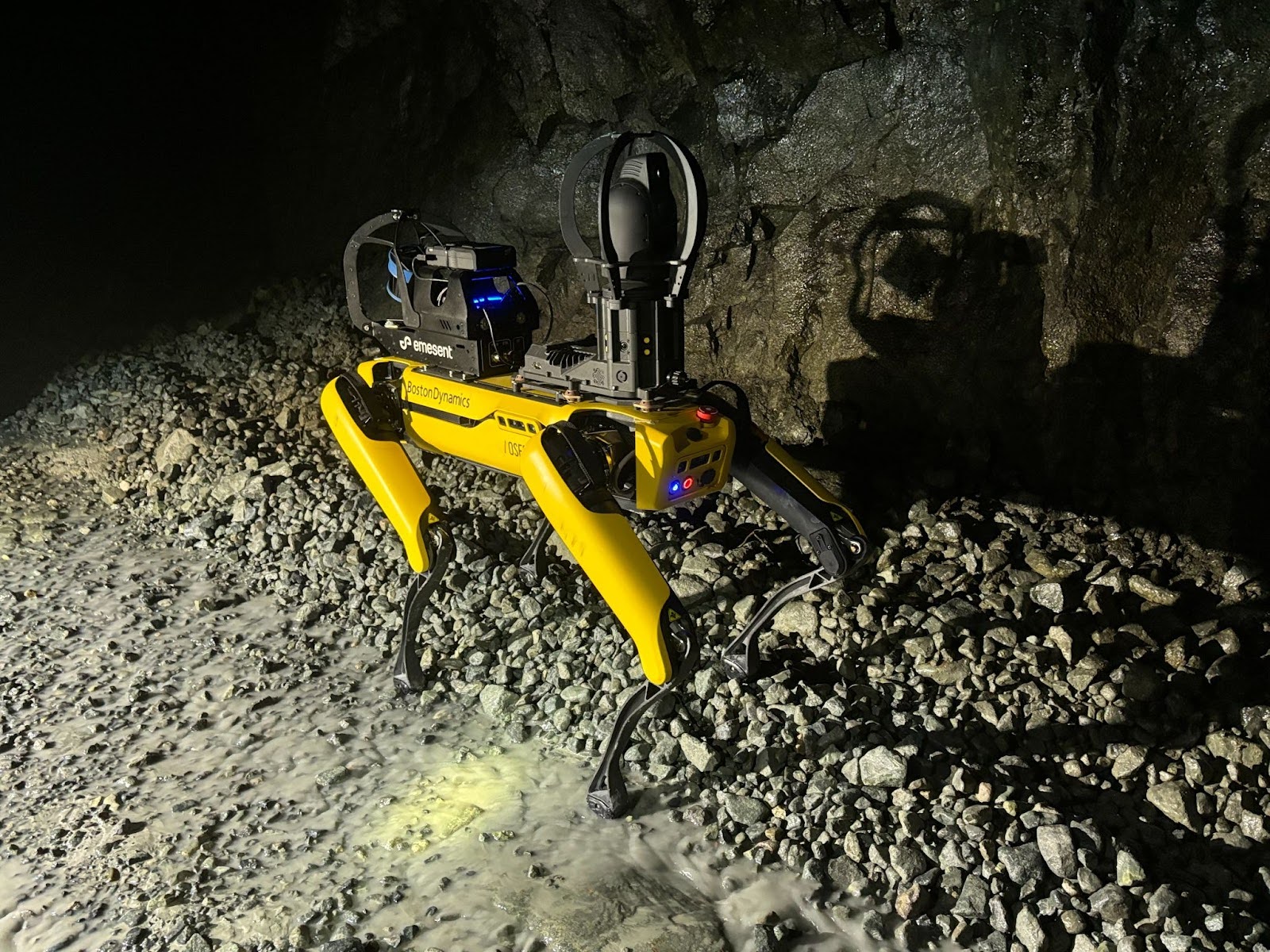
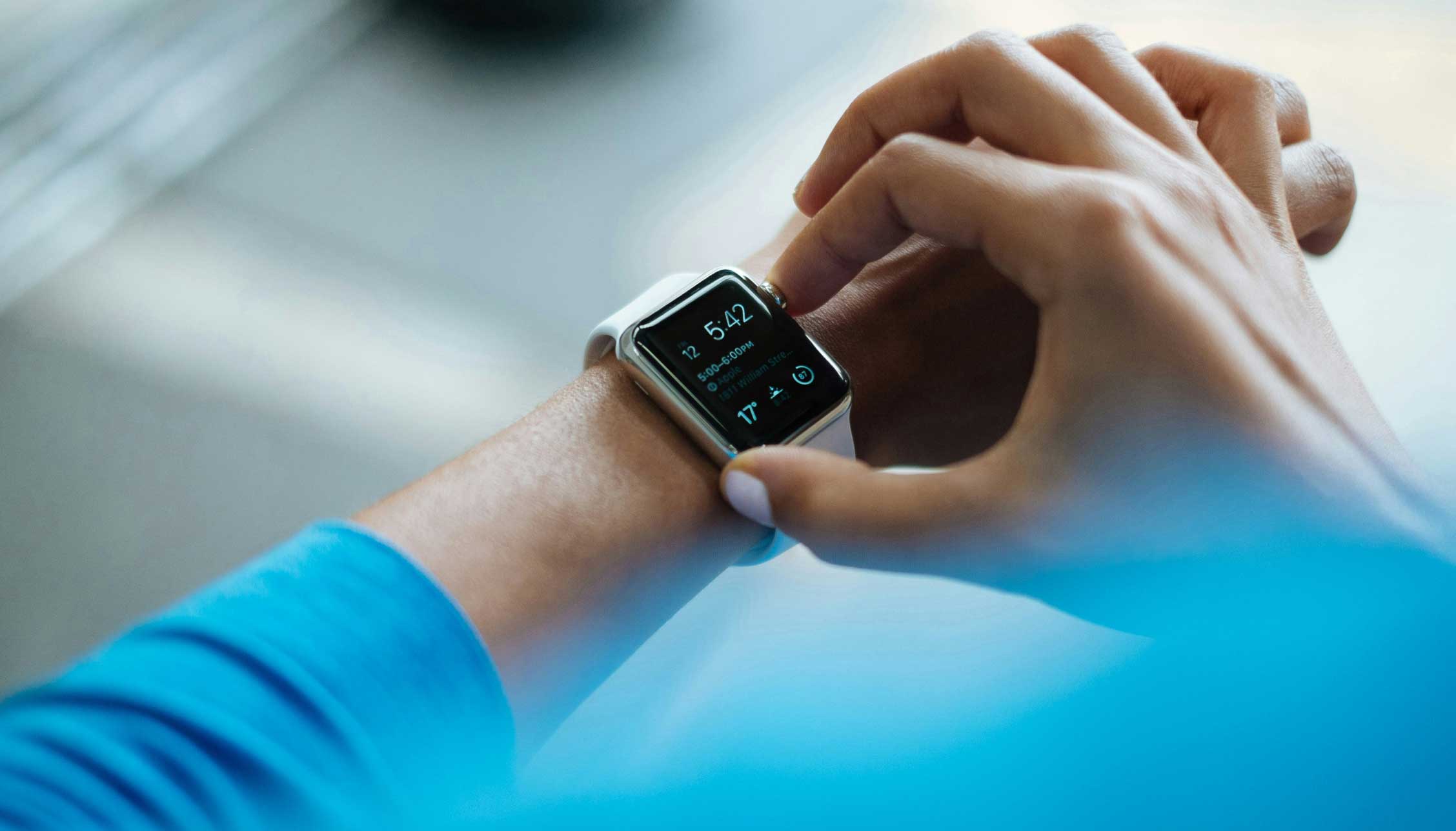
It doesn’t stop there for Spot
Spot can handle payloads of up to 14 kg (additional hardware for further value-added), meaning it can carry more than just the Hovermap ST-X. This opens up possibilities for additional capabilities, such as simultaneously collecting data on air quality, detecting abnormal levels of toxic gasses, or monitoring temperature. These added functionalities allow operators to remotely inspect newly blasted stopes or other areas that might contain hazardous levels of toxic gasses. Spot, unaffected by these conditions, can even alert operators when gas levels reach predefined thresholds.
In conclusion
Boston Dynamics has developed a highly versatile and dynamic sensing platform, and when paired with the Emesent Hovermap ST-X, it can significantly enhance mining operations. These improvements are not only limited to cost savings but also extend to ensuring greater safety for your personnel.
At Osedea, we can offer proof of concept with Spot to determine if it’s the right tool for you and your business. Send us a message—we’d love to discuss how we can collaborate!
Did this article start to give you some ideas? We’d love to work with you! Get in touch and let’s discover what we can do together.